Ford uses this new 3D printing center for the first electric Ford built in Europe
12 printers
In the new 3D printing center, 12 advanced 3D printers produce all kinds of plastic and metal parts. These range from parts only a few centimeters long and weighing 30 grams, to parts 2.4 meters long, 1.2 meters wide and 1 meter high weighing 15 kilograms, produced by the center’s largest 3D printer.
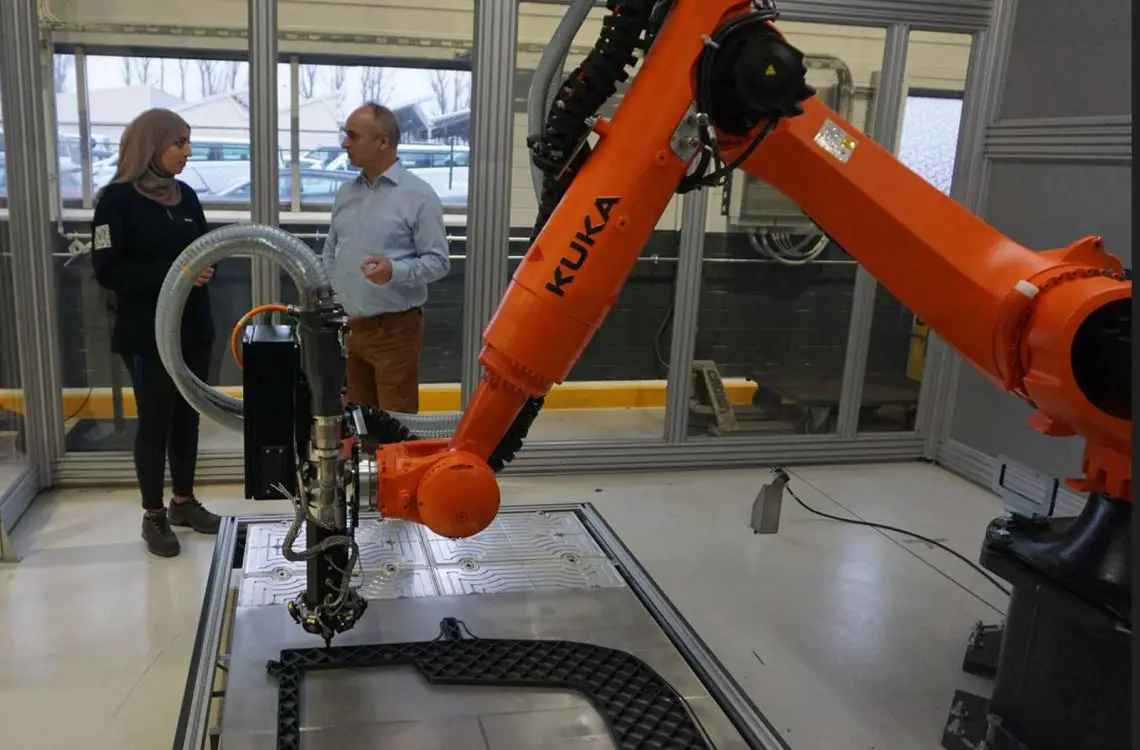
Sustainable
With 3D printing, the brand can not only produce complex parts, but also save time and money on small quantities: up to 80% compared to the conventional injection molding process. Especially making the necessary mold is very complicated. There is also a sustainability aspect to it: 3D printing requires significantly less material, and grain residue can be reused.
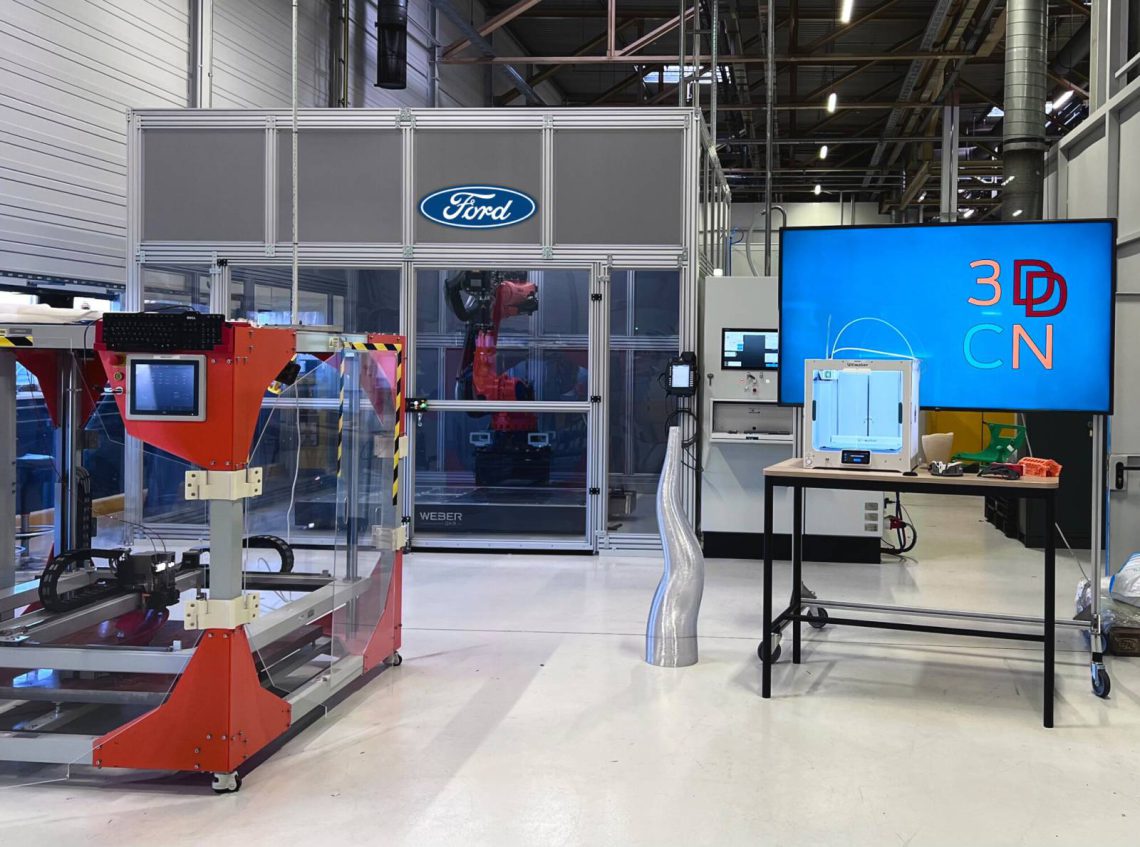
Experience
The brand already has a lot of experience with 3D printing. The Ford plant in Valencia has a special team in its 3D printing lab compiling a catalog of 5,000 printable parts. These provide solutions for different stages of the manufacturing process in the plant. In 2021 alone, the department made a total of 20,000 printed parts. At the Cologne plant, any Ford employee can submit an application through an app. In doing so, they can include their own drawing of the desired part or a description of what they need it for.
This timelapse video shows a holder for sheet metal samples being made at Ford’s 3D printing center: