Hoe Audi aan de fabriek van de toekomst werkt
Lopende band
Henry Ford wordt door velen gezien als de uitvinder van het lopendebandprincipe. De uitvinder en ondernemer kwam op het idee nadat hij een productielijn in een varkensslachterij in Chicago zag. Daar werden karkassen langs een productielijn vervoerd door een fabriek, waar één voor één ‘onderdelen’ vanaf werd gesneden. Helemaal origineel is het idee dus niet van Ford, maar hij was wel de eerste die het principe perfectioneerde en gebruikte om op grote schaal producten in elkaar te zetten.
Het chassis van de T-Ford werd met een touw door de fabriek getrokken en onderweg werden de onderdelen op de auto gemonteerd. Het bleek een meesterzet, want de productie steeg van 19.000 auto’s in 1908 tot 308.000 in 1914. De behoeftes van de mens werden hierbij echter niet meegenomen. Iedere dag duizendmaal dezelfde handeling uitvoeren is haast mensonterend. Gelukkig betaalde Ford goed, maar veel werknemers hielden het maar kort vol. Tegenwoordig doen robots het meeste werk in een autofabriek. Op plekken waar nog wél handen nodig zijn, wisselen werknemers vaak van ‘werkstation’, zodat het goed vol te houden is. Bij Audi gaan ze nog een stapje verder.
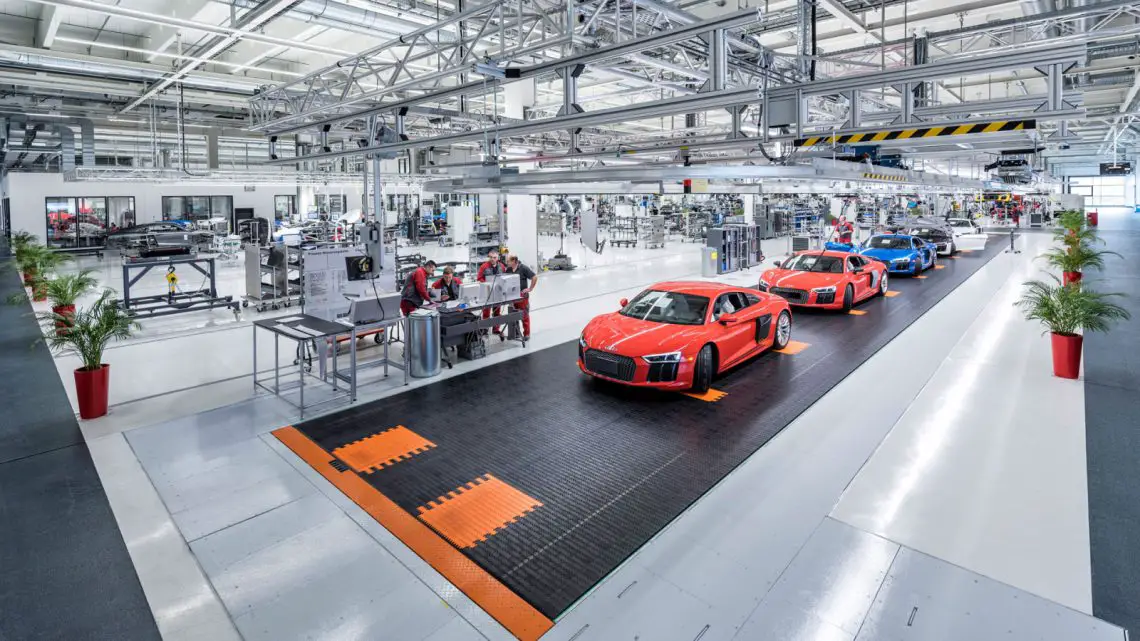
Modular Assembly
Audi introduceert als eerste automaker een modulaire productielijn. In een middelgrote productiehal in Ingolstadt, vol met zelfsturende robotkarretjes, zien we hoe het werkt. Op de karretjes die kriskras door de hal rijden staan verschillende auto-onderdelen, bijvoorbeeld deurpanelen. De karretjes rijden zelf naar het juiste werkstation en wachten daar tot een arbeider het onderdeel dat ze vervoeren verder in elkaar zet. De zogeheten automated guided vehicles (AGV’s) vervoeren afwisselende onderdelen van een auto, zodat het werk niet monotoon en saai wordt. Hierdoor wordt fabricagetijd verkort en neemt de productiviteit tot 20% toe.
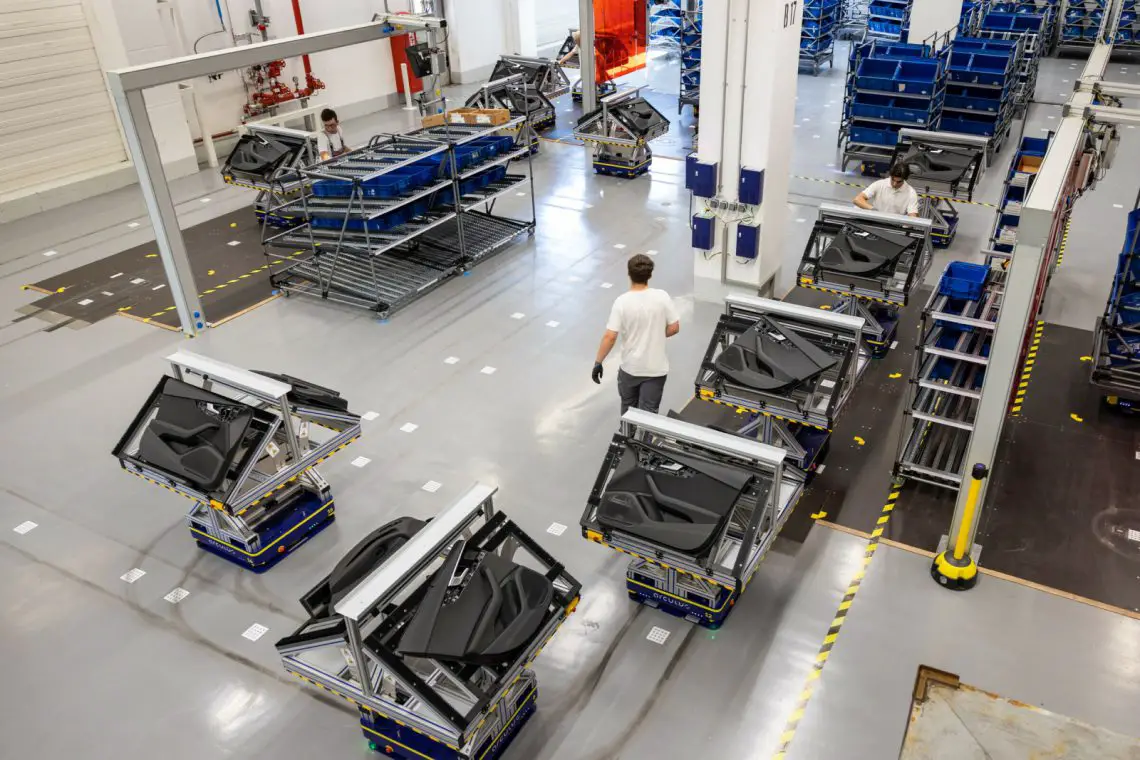
Fysieke beperkingen
Volgens Project Manager Wolfgang Kern brengt het systeem nog een ander groot voordeel met zich mee: Audi kan mensen inzetten die door fysieke beperkingen niet meer aan een normale productielijn kunnen werken. “We zijn in staat om de werkomgeving aan te passen aan hun omstandigheden, wat momenteel aan de lopende band slechts in zeer beperkte mate mogelijk is”, aldus Kern. “We gebruiken meer flexibele automatisering in het productieproces om mensen extra te ontlasten.”
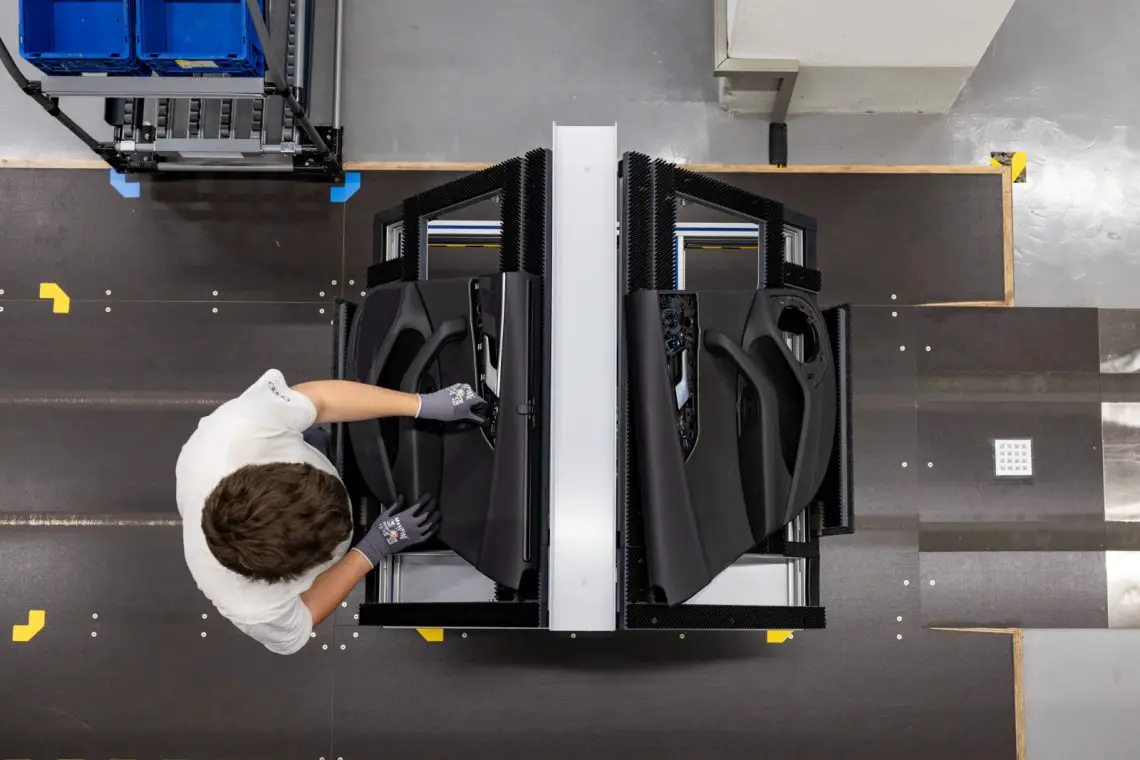
Robothond
In dezelfde hal maken we kennis met Spot, een robothond. Spot is een creatie van Boston Dynamics, een Amerikaans bedrijf gespecialiseerd in engineering en robotica. Spot gaat regelmatig viral op het internet, omdat de robot haast net een echte hond lijkt. Audi zet de gele hond in voor het inventariseren van de assemblagelijn. Vroeger kostte het medewerkers zo’n drie weken tijd om 100.000 m2 te inventariseren in de Audi-fabriek. Spot de robothond heeft hier slechts 48 uur voor nodig. Hij is wendbaar en kan zelf de weg door de fabriek vinden. Hij heeft ook geen slaap nodig, alleen af en toe een laadbeurt.
Hij is voorzien van een hightech scan-apparaat van het Duitse techbedrijf NavVis, dat de hele omgeving in 3D kan vastleggen. Het resultaat is een extreem gedetailleerde 3D-reconstructie van de fabriekshal. Alsof Google er met hun Maps-auto doorheen gereden is. Medewerkers kunnen zo op hun computer virtueel door de fabriek lopen en kijken of er ergens onderhoud nodig is, een likje verf of dat er onderdelen moeten worden bijgevuld.
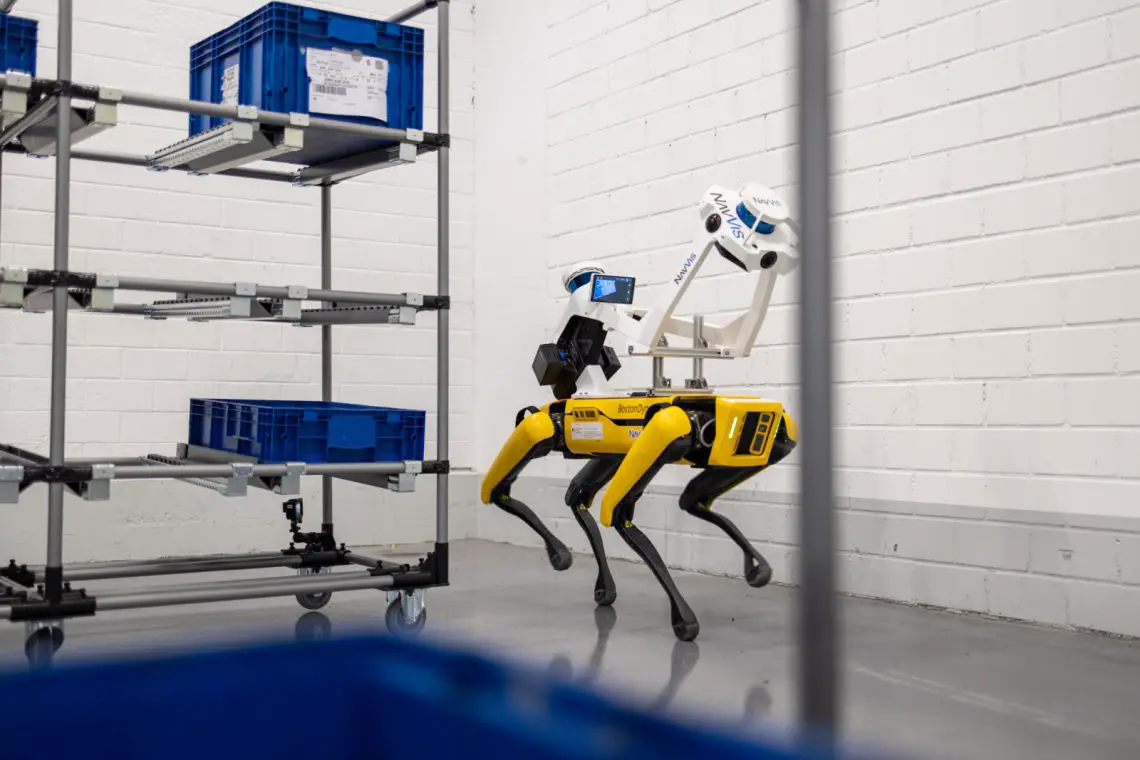
Artificial Intelligence
Er zijn meer saaie taken die in de Audi-fabriek niet meer door mensen worden uitgevoerd. Zo is het merk een proefproject gestart waarbij kunstmatige intelligentie (artificial intelligence, AI) de kwaliteit van puntlassen controleert. Er zijn ongeveer 5.300 laspunten nodig om de onderdelen in de carrosserie van een Audi A6 met elkaar te verbinden. Tot nu toe gebruikten de productiemedewerkers steekproefsgewijze ultrasone analyses om de kwaliteit van de puntlassen te controleren. Maar in het proefproject maken ze gebruik van AI om afwijkingen automatisch te herkennen, zonder dat de productieband stil moet worden gelegd.
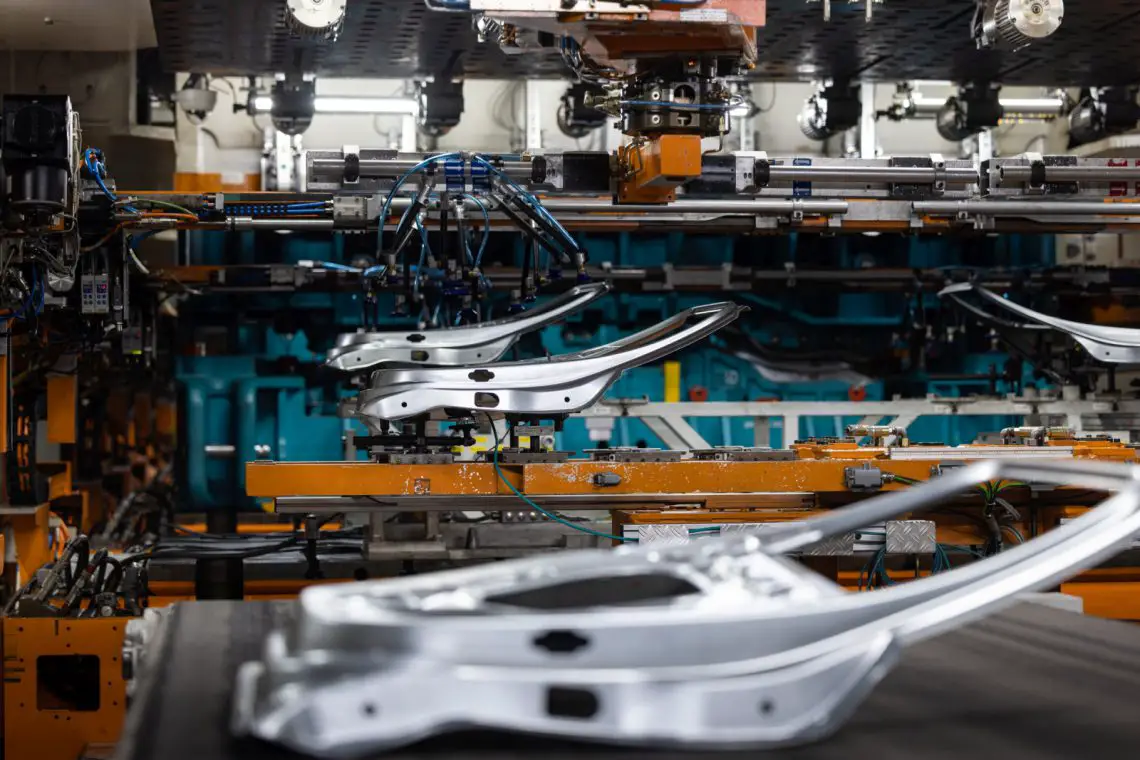
Duurzaamheid
De Audi-fabriek in Ingolstadt verbruikt in een jaar tijd ongeveer evenveel energie als een middelgrote stad. Het kost nou eenmaal veel energie om van een blok staal een rijdende auto te maken. Om energie te besparen heeft Audi de Energy Analytics-tool ontwikkeld. In de tool is alle energieconsumptie in de fabriek vastgelegd en inzichtelijk gemaakt. Dus bijvoorbeeld hoeveel energie de lasapparatuur verbruikt, maar ook wat de verlichting en ventilatie in de gebouwen gebruiken op een normale dag. Als het verbruik plotseling omhoog schiet, kunnen werknemers precies zien welke apparatuur daar verantwoordelijk voor is en meteen stappen ondernemen. In 2021 kon de Energy Analytics-tool al regelmatig onnodig stroomverbruik detecteren, waardoor er 37.000 MWh werd bespaard. Daar kun je heel wat kilometers mee maken in een Audi E-Tron GT.