Cómo trabaja Audi en la fábrica del futuro
Cinta transportadora
Muchos consideran a Henry Ford el inventor del principio de la cadena de montaje. El inventor y empresario tuvo la idea después de ver una línea de producción en un matadero de cerdos en Chicago. Allí, los cadáveres eran transportados a lo largo de una línea de producción a través de una fábrica, de la que se cortaban «partes» una a una. Así que la idea de Ford no es del todo original, pero fue el primero en perfeccionar el principio y utilizarlo para ensamblar productos a gran escala.
El chasis del T-Ford era arrastrado por la fábrica con una cuerda y las piezas se montaban en el coche por el camino. Resultó ser un golpe maestro, ya que la producción pasó de 19.000 coches en 1908 a 308.000 en 1914. Sin embargo, no se tuvieron en cuenta las necesidades de las personas. Hacer lo mismo mil veces cada día es casi degradante. Afortunadamente, Ford pagaba bien, pero muchos trabajadores duraban poco tiempo. Hoy en día, los robots hacen la mayor parte del trabajo en una fábrica de automóviles. En los lugares en los que todavía se necesitan manos, los trabajadores suelen cambiar de «puesto de trabajo», para que sea fácil seguir el ritmo. En Audi van un paso más allá.
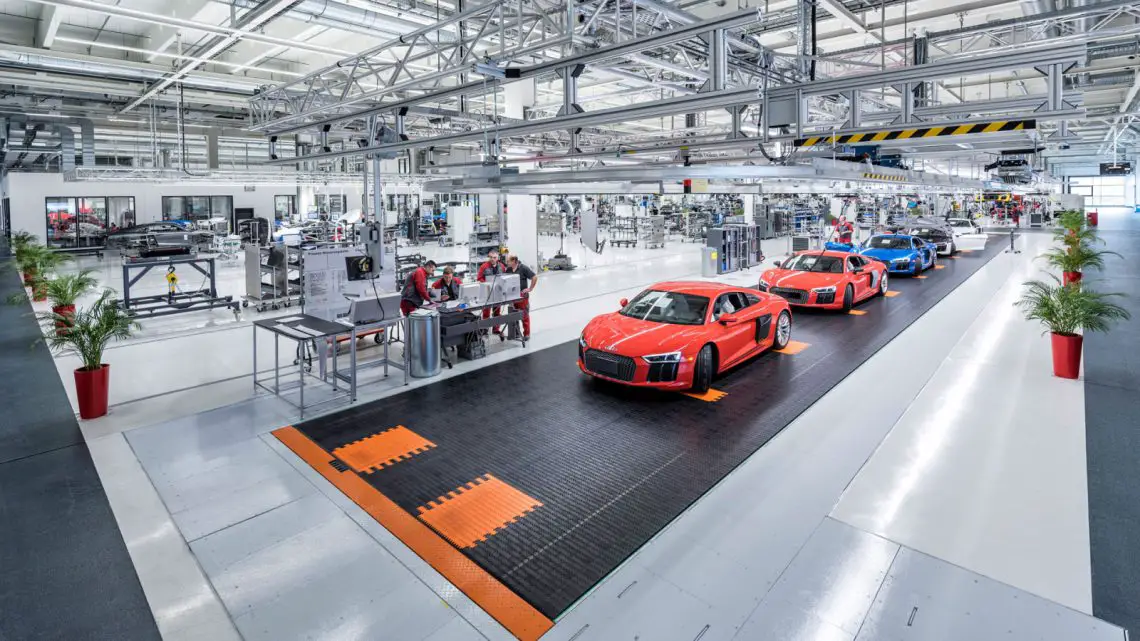
Montaje modular
Audi es el primer fabricante de automóviles que introduce una línea de producción modular. En una nave de producción de tamaño medio en Ingolstadt, llena de carros robotizados autodirigidos, vemos cómo funciona. En los carros que atraviesan la sala se exponen diversas piezas de automóviles, como los paneles de las puertas. Los carros se dirigen por sí mismos al puesto de trabajo adecuado y esperan allí a que un trabajador siga montando la pieza que transportan. Los llamados vehículos de guiado automático (AGV) transportan partes alternas de un coche, para que el trabajo no se vuelva monótono y aburrido. Esto acorta el tiempo de fabricación y aumenta la productividad hasta un 20%.
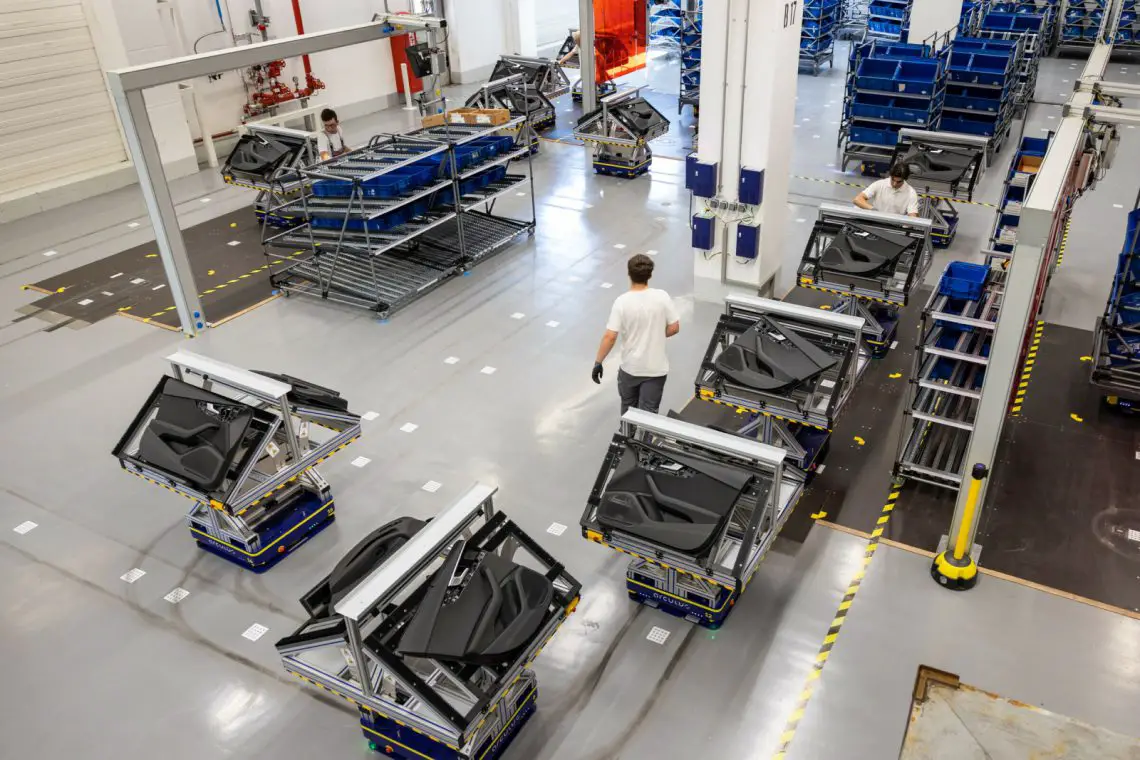
Limitaciones físicas
Según el director del proyecto, Wolfgang Kern, el sistema tiene otra gran ventaja: Audi puede emplear a personas que ya no pueden trabajar en una línea de producción normal debido a sus limitaciones físicas. «Podemos adaptar el entorno de trabajo a sus circunstancias, lo que actualmente sólo es posible de forma muy limitada en la cadena de montaje», afirma Kern. «Utilizamos una automatización más flexible en el proceso de producción para aliviar la carga adicional de las personas».
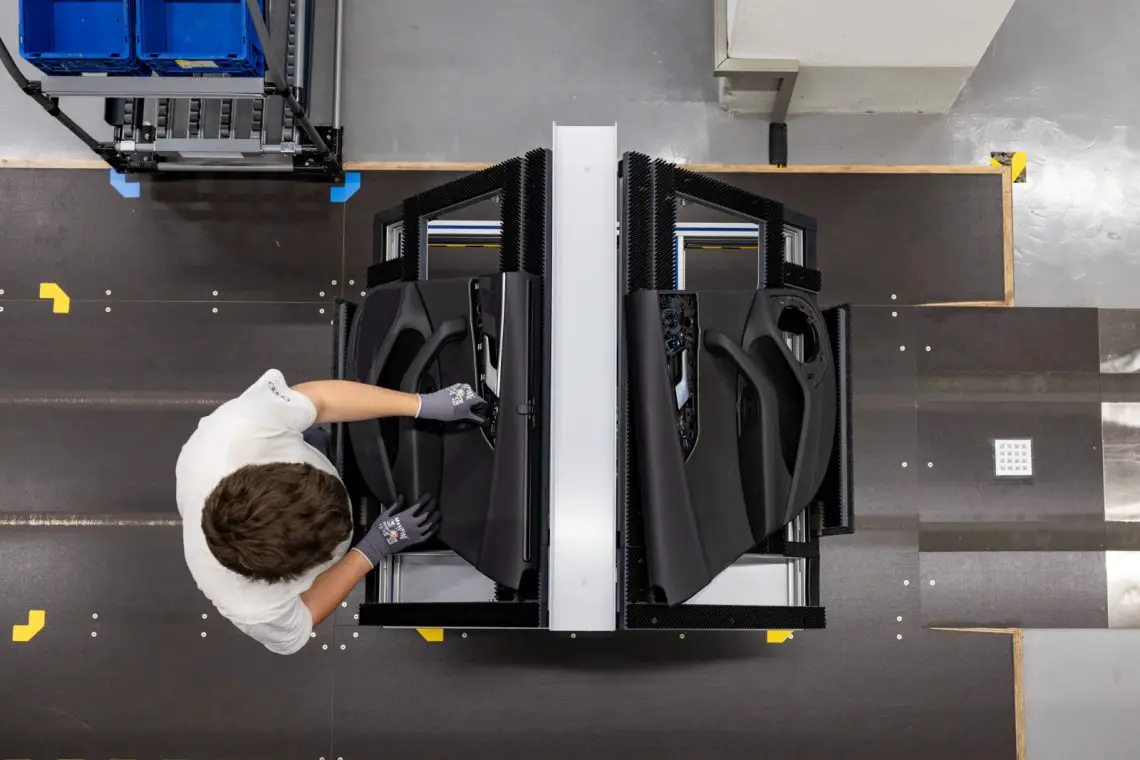
Perro robot
En la misma sala, conocemos a Spot, un perro robot. Spot es una creación de Boston Dynamics, una empresa estadounidense especializada en ingeniería y robótica. Spot se convierte regularmente en viral en Internet porque el robot casi se parece a un perro de verdad. Audi utiliza el perro amarillo para hacer un balance de la cadena de montaje. En el pasado, los empleados tardaban unas tres semanas en inventariar 100.000 m2 en la fábrica de Audi. El perro robot Spot sólo necesita 48 horas para hacerlo. Es maniobrable y puede encontrar su propio camino en la fábrica. Tampoco necesita dormir, sólo cargarse de vez en cuando.
Está equipado con un dispositivo de escaneo de alta tecnología de la empresa tecnológica alemana NavVis, que puede capturar todo el entorno en 3D. El resultado es una reconstrucción en 3D extremadamente detallada de la nave industrial. Como si Google lo hubiera atravesado con su coche de Maps. Los empleados pueden recorrer virtualmente la fábrica a través de sus ordenadores y ver si hay que reponer piezas de mantenimiento, pintura o repuestos.
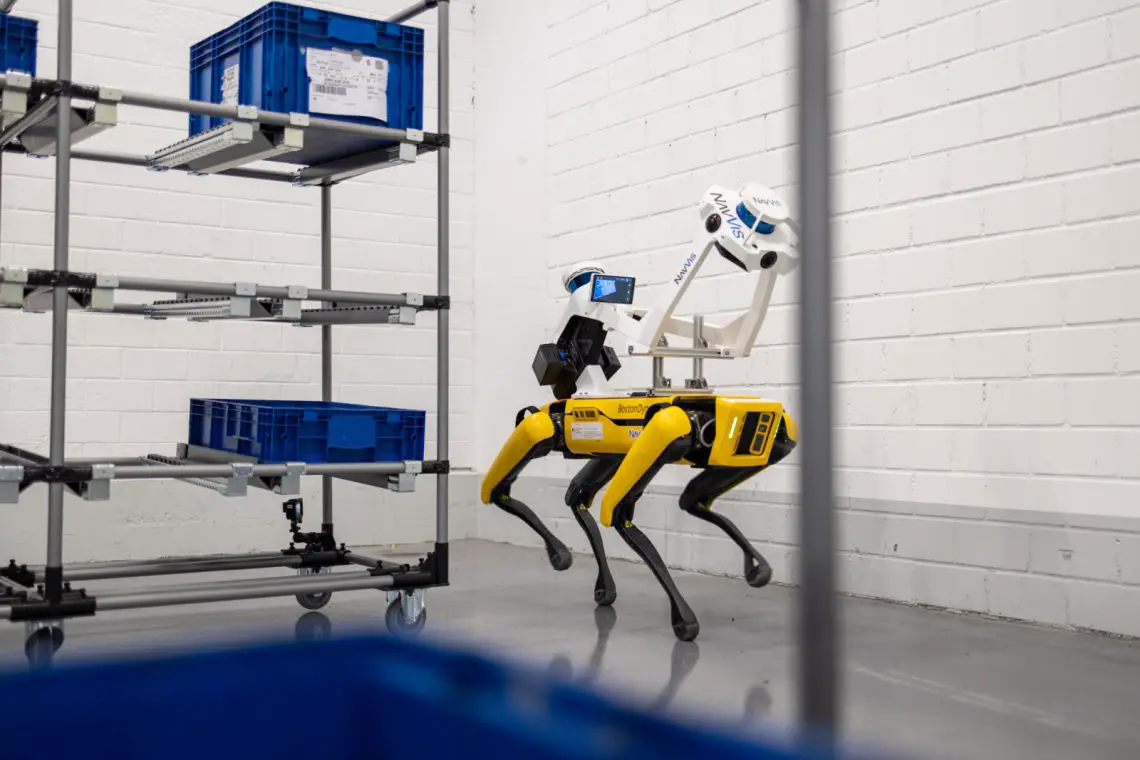
Inteligencia Artificial
Hay más tareas aburridas que ya no se realizan en la fábrica de Audi. Por ejemplo, la marca ha iniciado un proyecto piloto en el que la inteligencia artificial (IA) comprueba la calidad de las soldaduras por puntos. Para unir las piezas de la carrocería de un Audi A6 son necesarios unos 5.300 puntos de soldadura. Hasta ahora, el personal de producción utilizaba análisis ultrasónicos aleatorios para comprobar la calidad de los puntos de soldadura. Pero en el proyecto piloto, están utilizando la IA para reconocer las desviaciones automáticamente, sin tener que parar la línea de producción.
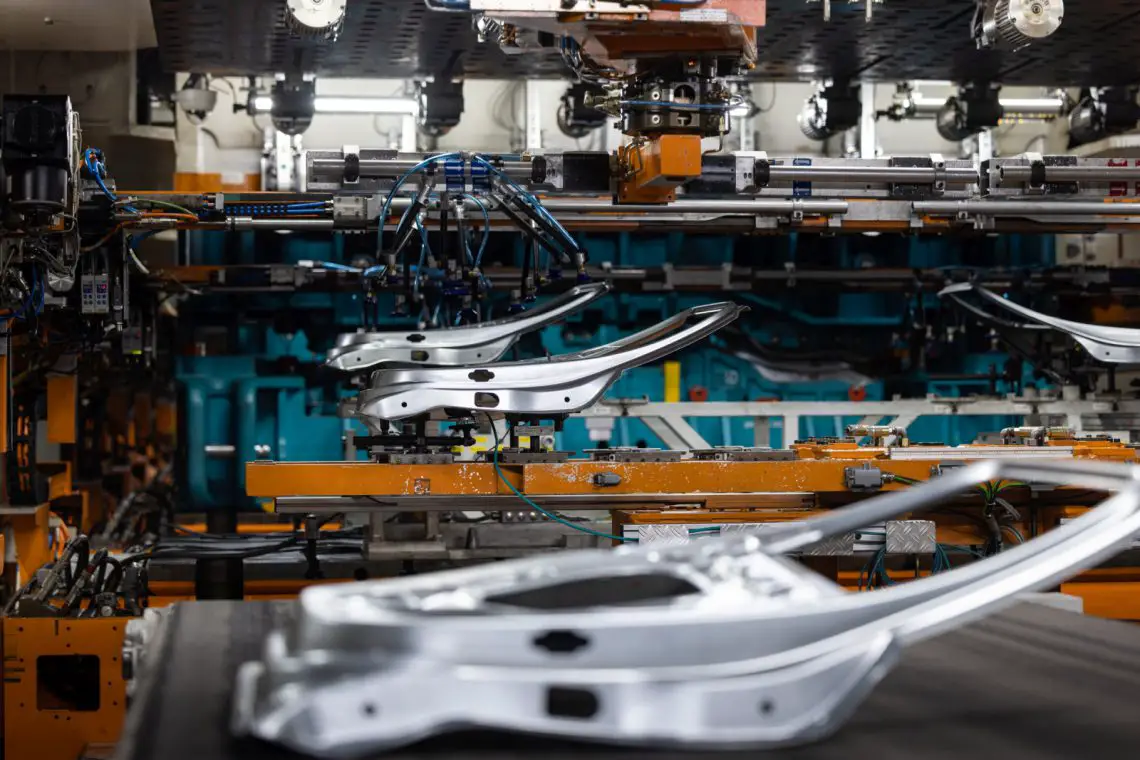
Sostenibilidad
La fábrica de Audi en Ingolstadt consume en un año tanta energía como una ciudad de tamaño medio. Después de todo, se necesita mucha energía para convertir un bloque de acero en un coche en movimiento. Para ahorrar energía, Audi ha desarrollado la herramienta Energy Analytics. En la herramienta, todo el consumo de energía de la planta se registra y se hace transparente. Así, por ejemplo, cuánta energía consume el equipo de soldadura, pero también lo que consumen la iluminación y la ventilación de los edificios en un día normal. Si el consumo se dispara de repente, los empleados pueden ver exactamente qué equipo es el responsable y tomar medidas inmediatamente. En 2021, la herramienta Energy Analytics ya era capaz de detectar regularmente el consumo innecesario de energía, ahorrando 37.000 MWh. Se puede sacar mucho provecho de eso en un Audi E-Tron GT.