How Audi is working on the factory of the future
Conveyor belt
Henry Ford is considered by many to be the inventor of the assembly line principle. The inventor and entrepreneur came up with the idea after seeing a production line in a pig slaughterhouse in Chicago. There, carcasses were transported along a production line through a factory, where one by one “parts” were cut from them. So the idea is not entirely original to Ford, but he was the first to perfect the principle and use it to assemble products on a large scale.
The chassis of the T-Ford was pulled by a rope through the factory, and parts were assembled on the car along the way. It proved to be a masterstroke, as production rose from 19,000 cars in 1908 to 308,000 in 1914. However, this did not include the needs of humans. Performing the same action a thousand times every day is almost degrading. Fortunately, Ford paid well, but many workers lasted only a short time. Today, robots do most of the work in a car factory. In places where hands are still needed, employees often change ‘workstations’, so that it is easy to keep up. At Audi, they go one step further.
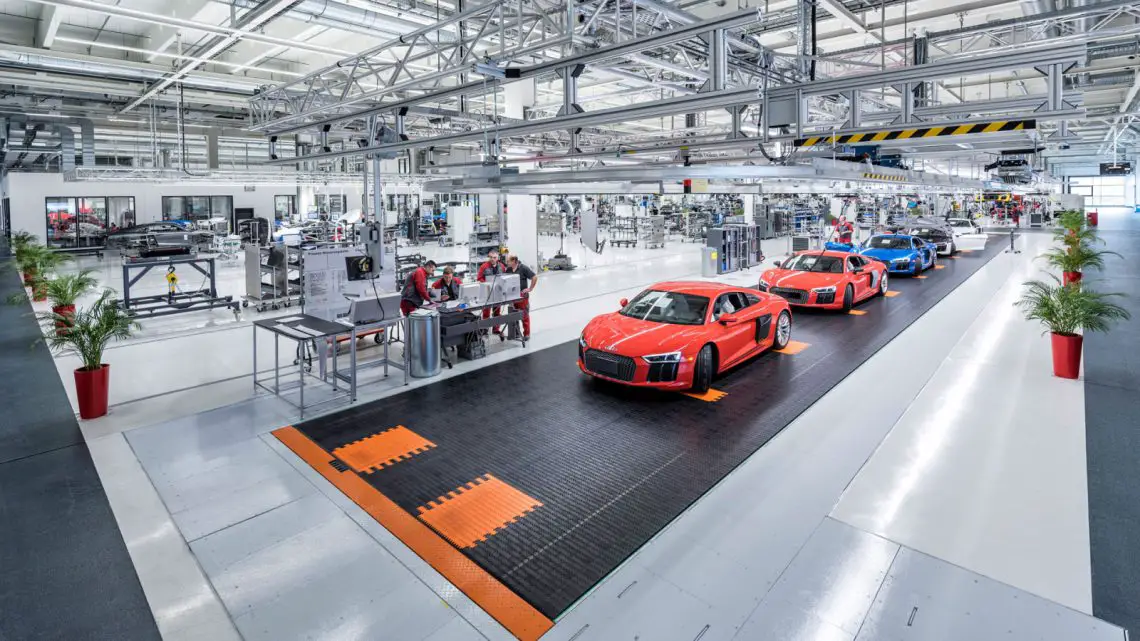
Modular Assembly
Audi is the first automaker to introduce a modular production line. In a medium-sized production hall in Ingolstadt, filled with self-steering robot carts, we see how it works. On the carts crisscrossing the hall are various car parts, for example door panels. The carts drive themselves to the appropriate workstation and wait there for a worker to further assemble the part they are carrying. The so-called automated guided vehicles (AGVs) transport alternate parts of a car so that the work does not become monotonous and boring. This reduces manufacturing time and increases productivity by up to 20%.
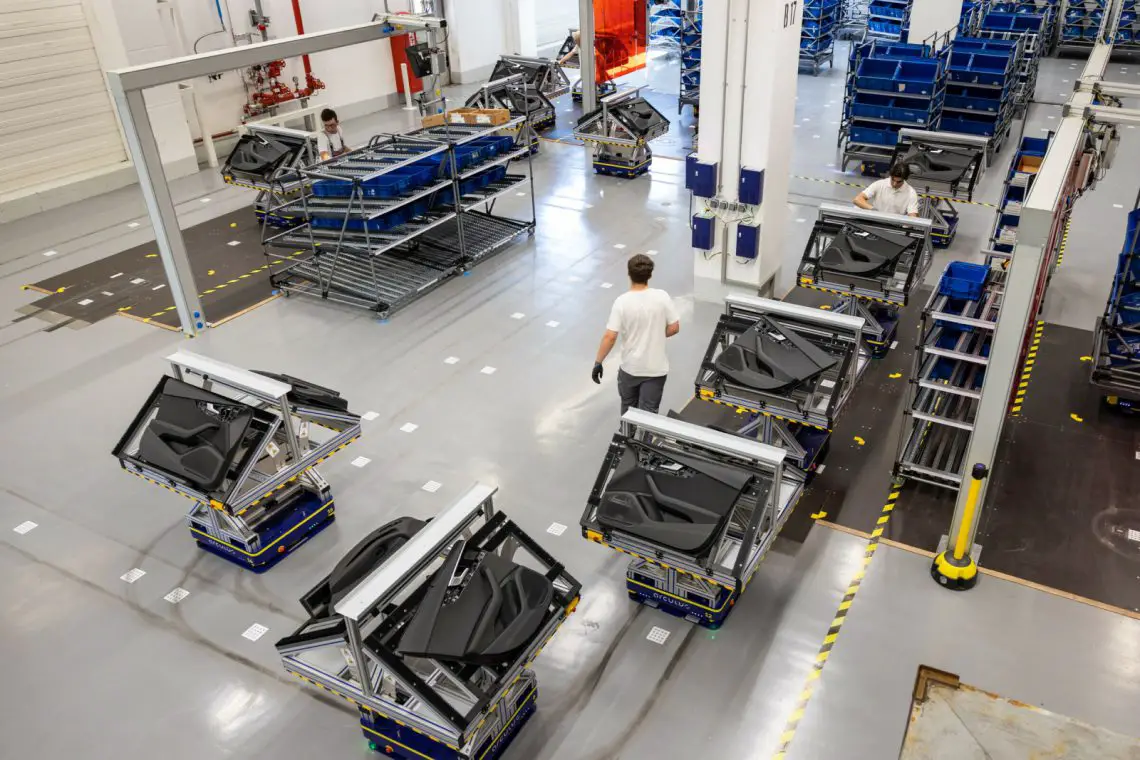
Physical Limitations
According to Project Manager Wolfgang Kern, the system brings another major benefit: Audi can employ people who can no longer work on a normal production line due to physical limitations. “We are able to adapt the work environment to their circumstances, which is currently only possible to a very limited extent on the assembly line,” Kern said. “We are using more flexible automation in the production process to give people additional relief.”
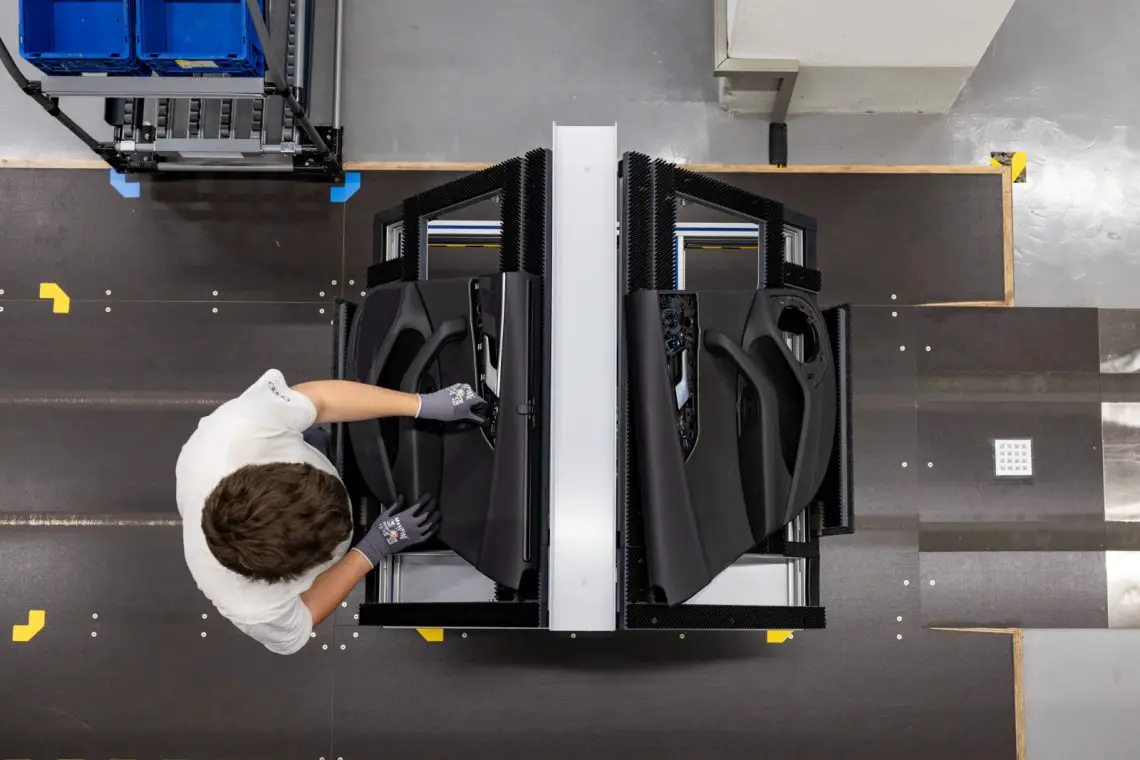
Robot Dog
In the same hall, we are introduced to Spot, a robot dog. Spot is a creation of Boston Dynamics, an American company specializing in engineering and robotics. Spot regularly goes viral on the Internet because the robot almost looks like a real dog. Audi deploys the yellow dog to inventory the assembly line. It used to take employees about three weeks to inventory 100,000 square meters at the Audi plant. Spot the robot dog needs only 48 hours to do this. It is maneuverable and can find its own way around the plant. It also doesn’t need sleep, just occasional charging.
It is equipped with a high-tech scanning device from German tech company NavVis, which can capture the entire environment in 3D. The result is an extremely detailed 3D reconstruction of the factory hall. As if Google had driven through it with their Maps car. Employees can thus virtually walk through the plant on their computers and see if any maintenance, a lick of paint or parts need to be refilled.
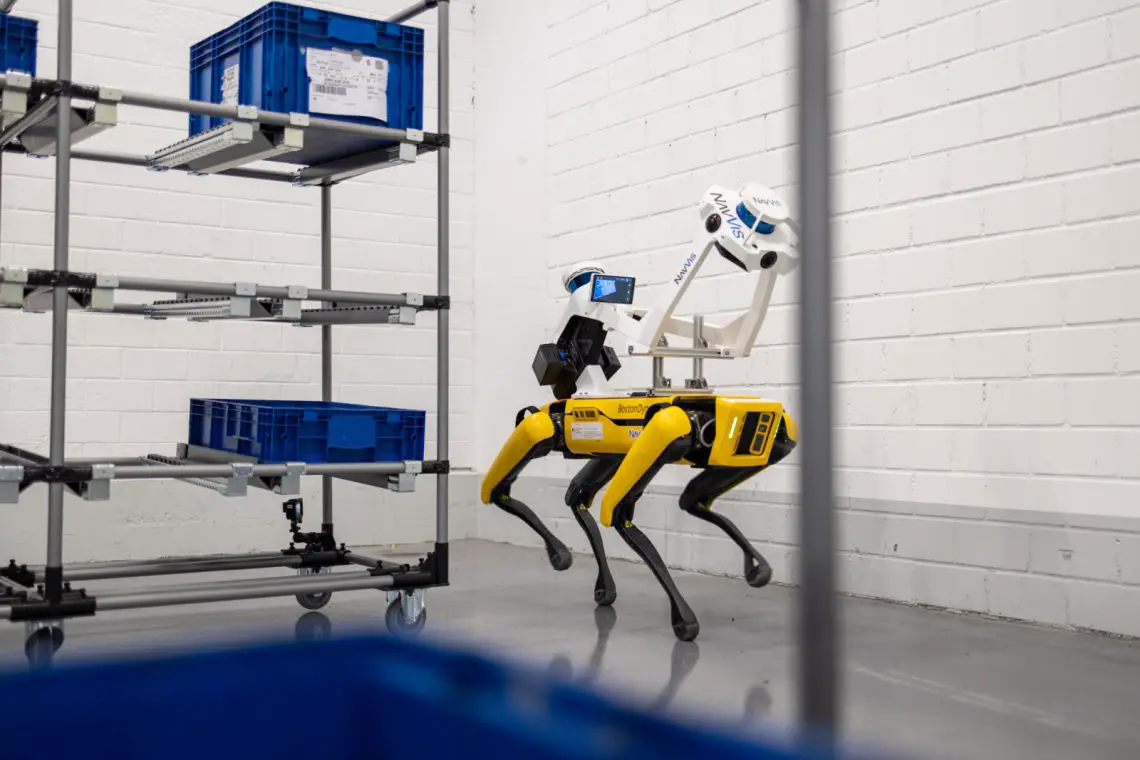
Artificial Intelligence
There are more boring tasks that are no longer performed by humans in the Audi factory. For example, the brand has launched a pilot project in which artificial intelligence (AI) checks the quality of spot welds. It takes about 5,300 welding points to connect the parts in the body of an Audi A6. Until now, production staff used random ultrasonic analysis to check the quality of spot welds. But in the pilot project, they are using AI to recognize deviations automatically, without having to stop the production line.
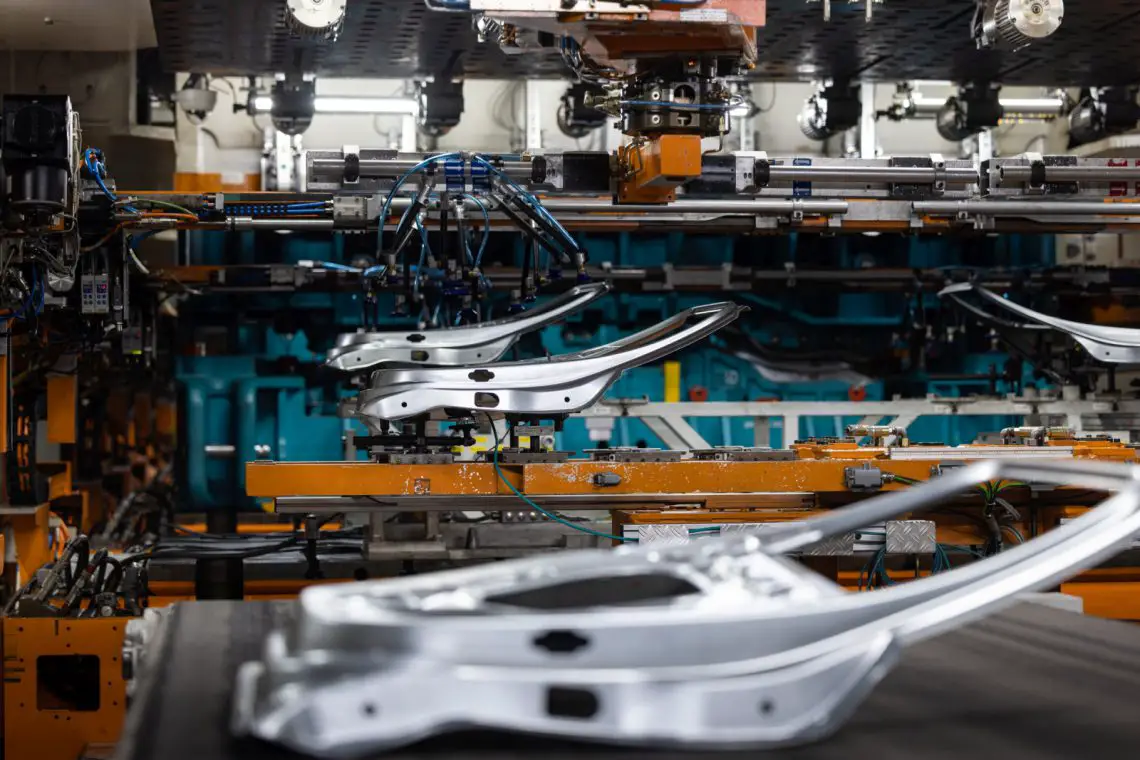
Sustainability
The Audi plant in Ingolstadt consumes about as much energy in a year as a medium-sized city. It does take a lot of energy to turn a block of steel into a moving car. To save energy, Audi has developed the Energy Analytics tool. In the tool, all energy consumption in the plant is recorded and made transparent. So for example, how much energy the welding equipment consumes, but also what the lighting and ventilation in the buildings use on a normal day. If consumption suddenly skyrockets, employees can see exactly which equipment is responsible and take immediate action. By 2021, the Energy Analytics tool was already able to regularly detect unnecessary power consumption, saving 37,000 MWh. You can get a lot of mileage out of that in an Audi E-Tron GT.