Comment Audi travaille sur l’usine du futur
Bande transporteuse
Henry Ford est considéré par beaucoup comme l’inventeur du principe de la chaîne de montage. L’inventeur et entrepreneur a eu cette idée après avoir vu une chaîne de production dans un abattoir de porcs à Chicago. Là, les carcasses étaient transportées le long d’une chaîne de production dans une usine, à partir de laquelle les « pièces » étaient découpées une par une. L’idée de Ford n’est donc pas entièrement originale, mais il a été le premier à perfectionner le principe et à l’utiliser pour assembler des produits à grande échelle.
Le châssis de la T-Ford était tiré par une corde à travers l’usine et les pièces étaient assemblées sur la voiture en cours de route. Ce fut un coup de maître, puisque la production passa de 19 000 voitures en 1908 à 308 000 en 1914. Cependant, les besoins des personnes n’ont pas été pris en compte. Faire la même chose mille fois par jour est presque dégradant. Heureusement, Ford payait bien, mais de nombreux travailleurs ne restaient que peu de temps. Aujourd’hui, les robots effectuent la majeure partie du travail dans une usine automobile. Dans les endroits où l’on a encore besoin de mains, les travailleurs changent souvent de « poste de travail », afin de pouvoir suivre le rythme. Chez Audi, ils vont encore plus loin.
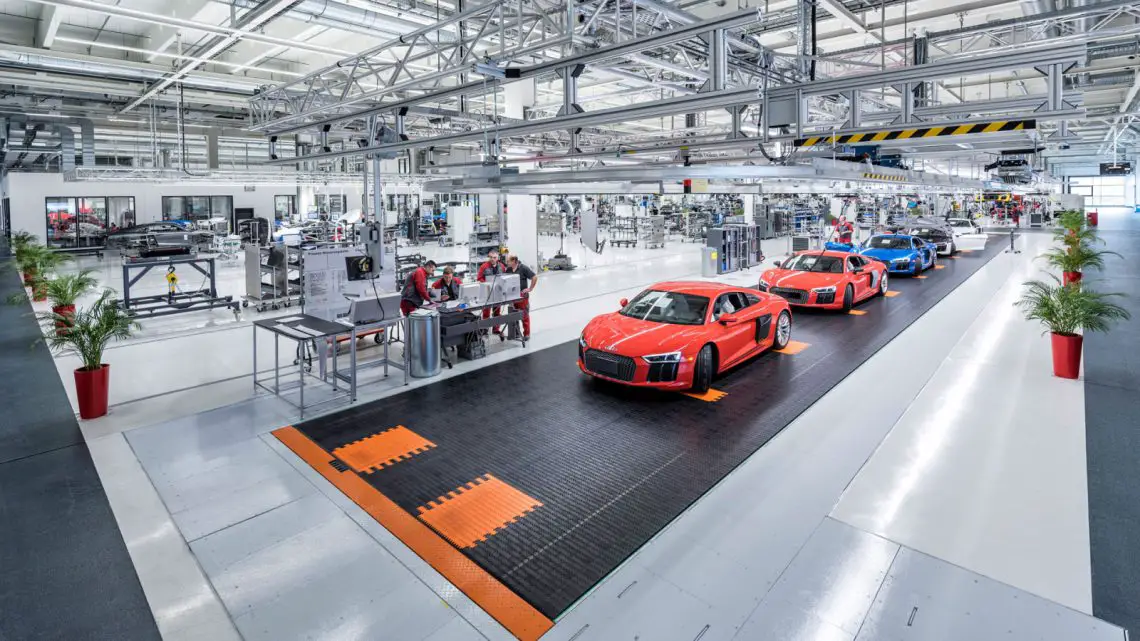
Assemblage modulaire
Audi est le premier constructeur automobile à introduire une ligne de production modulaire. Dans un hall de production de taille moyenne à Ingolstadt, rempli de chariots robots autoguidés, nous voyons comment cela fonctionne. Diverses pièces automobiles, par exemple des panneaux de porte, sont exposées sur les chariots qui sillonnent le hall. Les chariots se dirigent eux-mêmes vers le bon poste de travail et y attendent qu’un travailleur poursuive l’assemblage de la pièce qu’ils transportent. Les véhicules guidés automatisés (AGV) transportent les différentes parties d’une voiture, afin d’éviter que le travail ne devienne monotone et ennuyeux. Cela permet de réduire le temps de fabrication et d’augmenter la productivité jusqu’à 20 %.
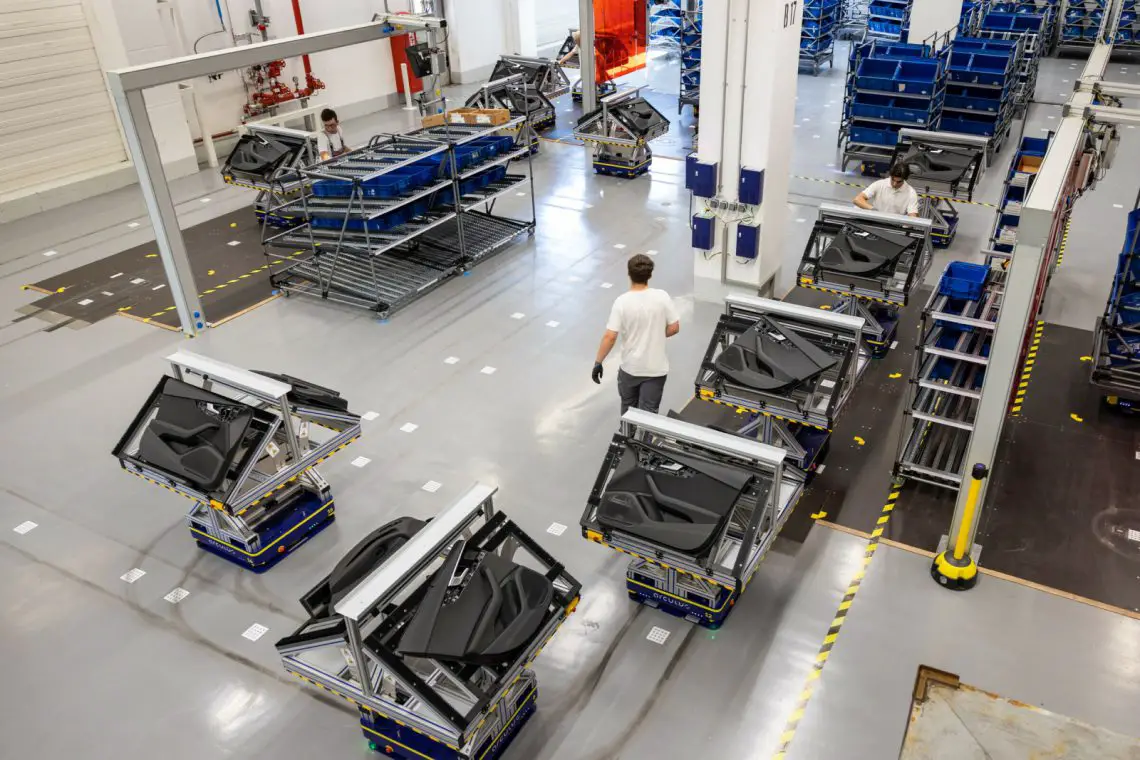
Limitations physiques
Selon le chef de projet Wolfgang Kern, le système présente un autre avantage majeur : Audi peut employer des personnes qui ne peuvent plus travailler sur une ligne de production normale en raison de limitations physiques. « Nous sommes en mesure d’adapter l’environnement de travail à leur situation, ce qui n’est actuellement possible que dans une mesure très limitée sur la chaîne de montage », explique M. Kern. « Nous utilisons une automatisation plus flexible dans le processus de production afin de soulager les personnes de la charge supplémentaire. »
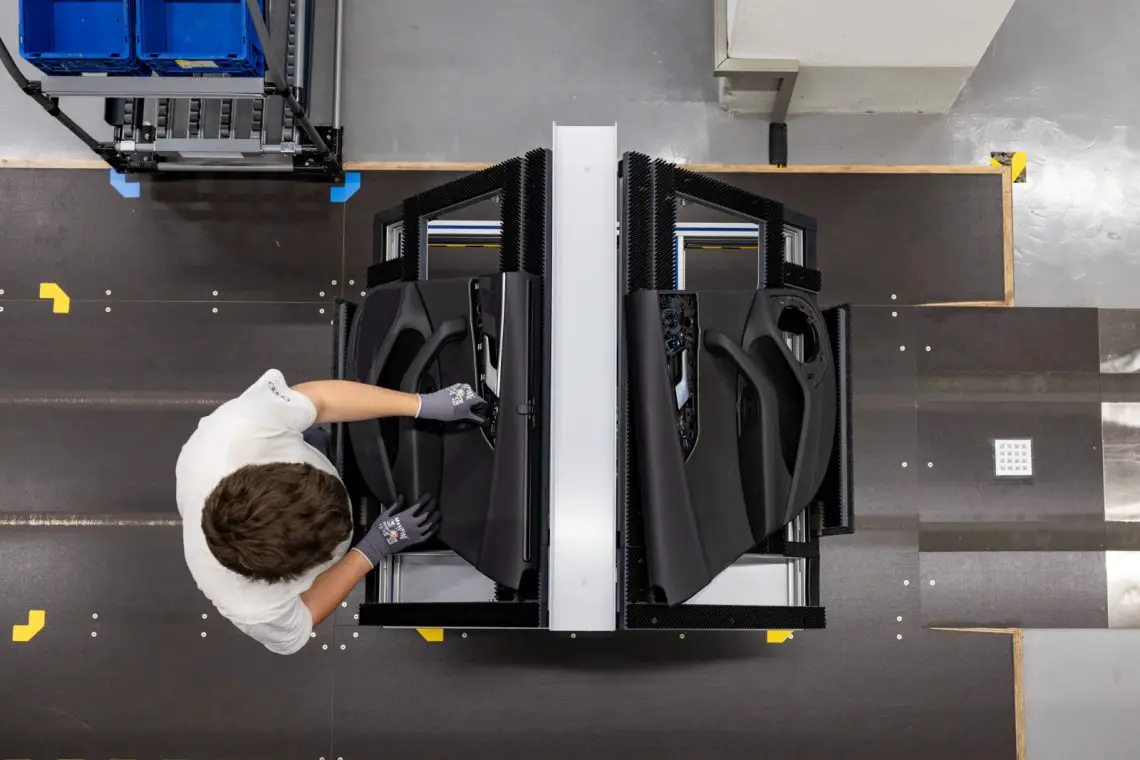
Chien robot
Dans la même salle, nous rencontrons Spot, un chien robot. Spot est une création de Boston Dynamics, une entreprise américaine spécialisée dans l’ingénierie et la robotique. Spot devient régulièrement viral sur Internet car le robot ressemble presque à un vrai chien. Audi utilise le chien jaune pour faire le point sur la chaîne de montage. Par le passé, il fallait environ trois semaines aux employés pour inventorier 100 000 m2 dans l’usine Audi. Spot le chien robot n’a besoin que de 48 heures pour le faire. Il est maniable et peut trouver son propre chemin dans l’usine. Il n’a pas besoin de dormir non plus, juste de se recharger occasionnellement.
Il est équipé d’un dispositif de balayage de haute technologie de la société allemande NavVis, qui peut capturer l’ensemble de l’environnement en 3D. Le résultat est une reconstruction 3D extrêmement détaillée du hall de l’usine. Comme si Google l’avait traversé avec sa voiture Maps. Les employés peuvent se promener virtuellement dans l’usine sur leur ordinateur et voir s’il faut réapprovisionner en maintenance, en peinture ou en pièces de rechange.
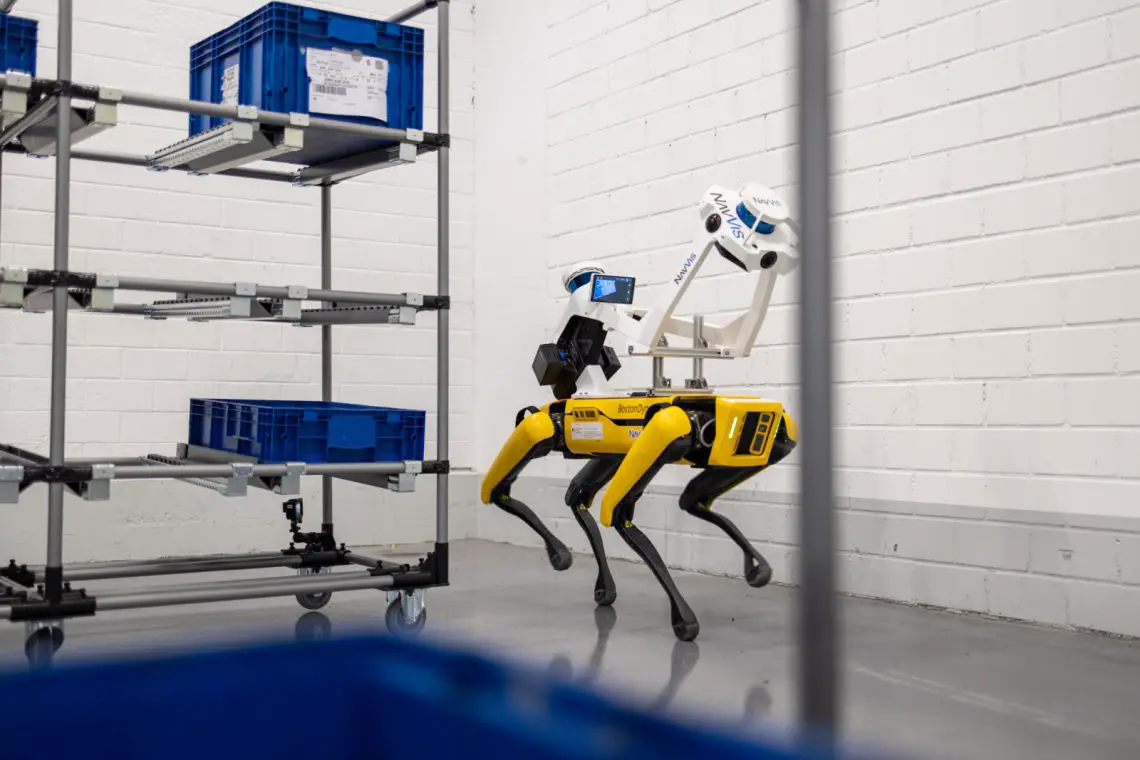
Intelligence artificielle
Il y a des tâches plus ennuyeuses qui ne sont plus effectuées par les gens de l’usine Audi. Par exemple, la marque a lancé un projet pilote dans lequel l’intelligence artificielle (IA) vérifie la qualité des soudures par points. Environ 5 300 points de soudure sont nécessaires pour relier les pièces de la carrosserie d’une Audi A6. Jusqu’à présent, le personnel de production utilisait des analyses ultrasoniques aléatoires pour vérifier la qualité des soudures par points. Mais dans le projet pilote, ils utilisent l’IA pour reconnaître automatiquement les écarts, sans avoir à arrêter la ligne de production.
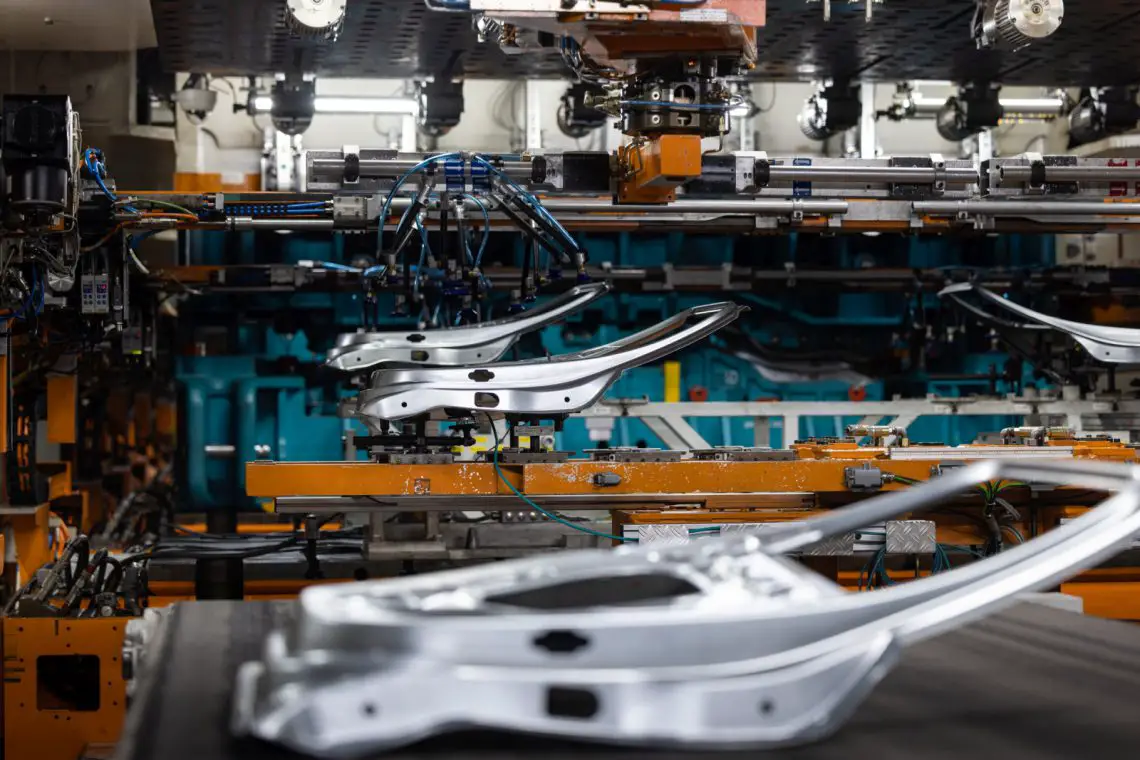
Durabilité
L’usine Audi d’Ingolstadt consomme en un an autant d’énergie qu’une ville de taille moyenne. Après tout, il faut beaucoup d’énergie pour transformer un bloc d’acier en une voiture en mouvement. Pour économiser l’énergie, Audi a développé l’outil Energy Analytics. Dans cet outil, toute la consommation d’énergie de l’usine est enregistrée et rendue transparente. Ainsi, par exemple, la quantité d’énergie consommée par les équipements de soudage, mais aussi la consommation de l’éclairage et de la ventilation des bâtiments au cours d’une journée normale. Si la consommation explose soudainement, les employés peuvent voir exactement quel équipement est responsable et prendre des mesures immédiatement. En 2021, l’outil d’analyse énergétique était déjà en mesure de détecter régulièrement les consommations électriques inutiles, permettant ainsi d’économiser 37 000 MWh. Vous pouvez en tirer beaucoup de kilomètres dans une Audi E-Tron GT.