Wie Audi an der Fabrik der Zukunft arbeitet
Förderband
Henry Ford wird von vielen als der Erfinder des Fließbandprinzips angesehen. Der Erfinder und Unternehmer kam auf die Idee, nachdem er eine Produktionsstraße in einem Schweineschlachthof in Chicago gesehen hatte. Dort wurden die Kadaver auf einem Fließband durch eine Fabrik transportiert, aus der die „Teile“ einzeln herausgeschnitten wurden. Fords Idee ist also nicht ganz originell, aber er war der erste, der das Prinzip perfektionierte und es für die Montage von Produkten in großem Maßstab einsetzte.
Das Chassis des T-Ford wurde mit einem Seil durch die Fabrik gezogen und die Teile wurden unterwegs am Auto montiert. Dies erwies sich als Meisterleistung, denn die Produktion stieg von 19.000 Autos im Jahr 1908 auf 308.000 im Jahr 1914. Die Bedürfnisse der Menschen wurden jedoch nicht berücksichtigt. Jeden Tag tausendmal das Gleiche zu tun, ist fast schon entwürdigend. Glücklicherweise bezahlte Ford gut, aber viele Arbeiter blieben nur kurze Zeit. Die meiste Arbeit in einer Autofabrik wird heute von Robotern erledigt. An Orten, an denen noch Hände gebraucht werden, wechseln die Arbeitnehmer häufig den „Arbeitsplatz“, so dass es einfach ist, mitzuhalten. Bei Audi geht man noch einen Schritt weiter.
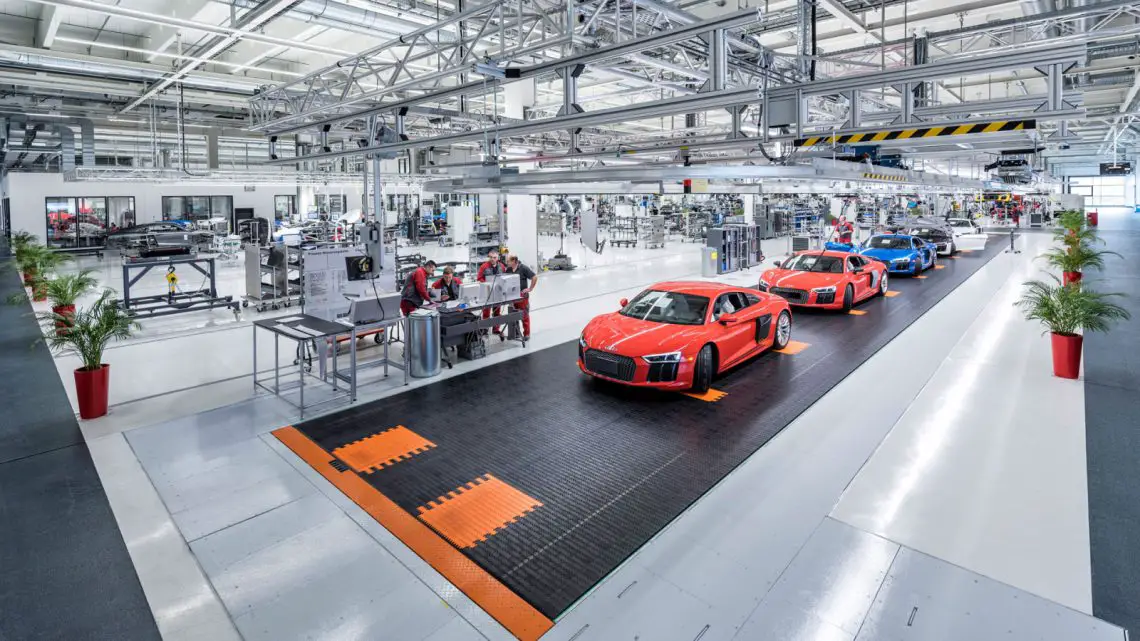
Modularer Aufbau
Audi ist der erste Automobilhersteller, der eine modulare Produktionslinie einführt. In einer mittelgroßen Produktionshalle in Ingolstadt, gefüllt mit selbstlenkenden Roboterwagen, sehen wir, wie es funktioniert. Verschiedene Autoteile, wie z. B. Türverkleidungen, sind auf den Wagen ausgestellt, die kreuz und quer durch die Halle fahren. Die Wagen fahren selbständig zum richtigen Arbeitsplatz und warten dort auf einen Arbeiter, der das Teil, das sie transportieren, weiter zusammenbaut. Die so genannten fahrerlosen Transportsysteme (AGVs) transportieren abwechselnd Teile eines Autos, damit die Arbeit nicht eintönig und langweilig wird. Dies verkürzt die Fertigungszeit und erhöht die Produktivität um bis zu 20 %.
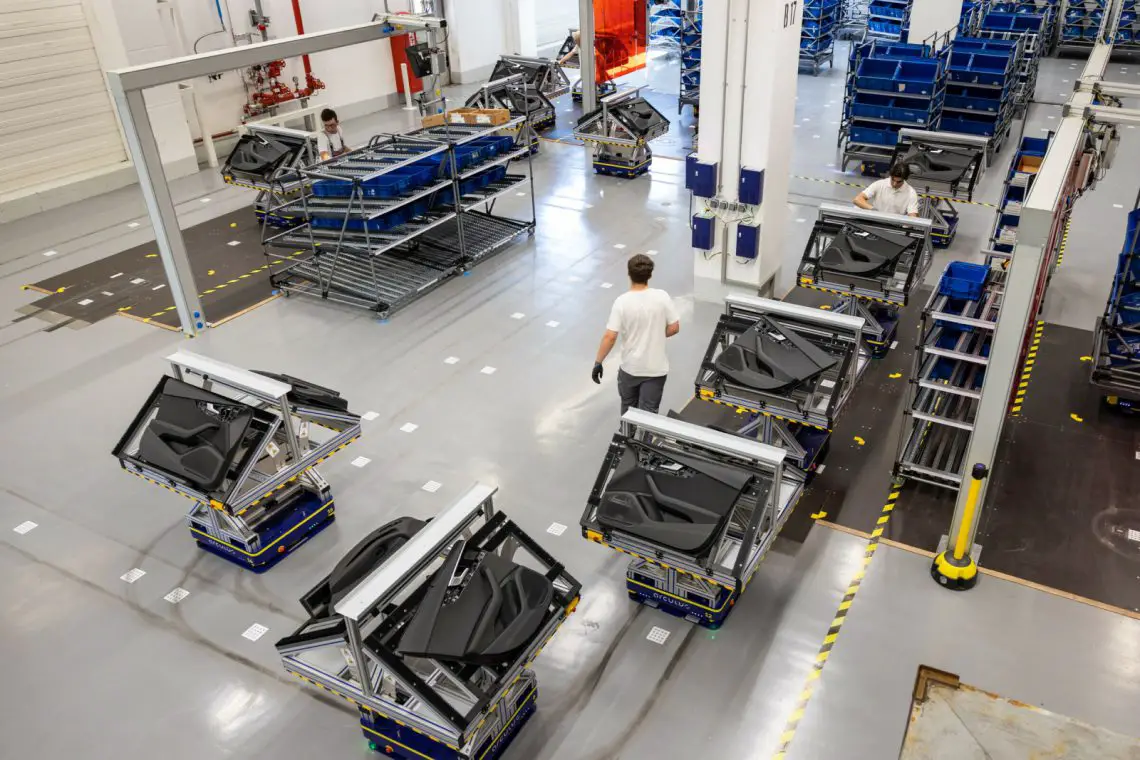
Körperliche Einschränkungen
Laut Projektleiter Wolfgang Kern hat das System einen weiteren großen Vorteil: Audi kann Menschen beschäftigen, die aufgrund körperlicher Einschränkungen nicht mehr an einer normalen Produktionslinie arbeiten können. „Wir sind in der Lage, das Arbeitsumfeld an die jeweiligen Gegebenheiten anzupassen, was am Fließband derzeit nur sehr eingeschränkt möglich ist“, sagt Kern. „Wir setzen eine flexiblere Automatisierung im Produktionsprozess ein, um die Menschen zu entlasten.“
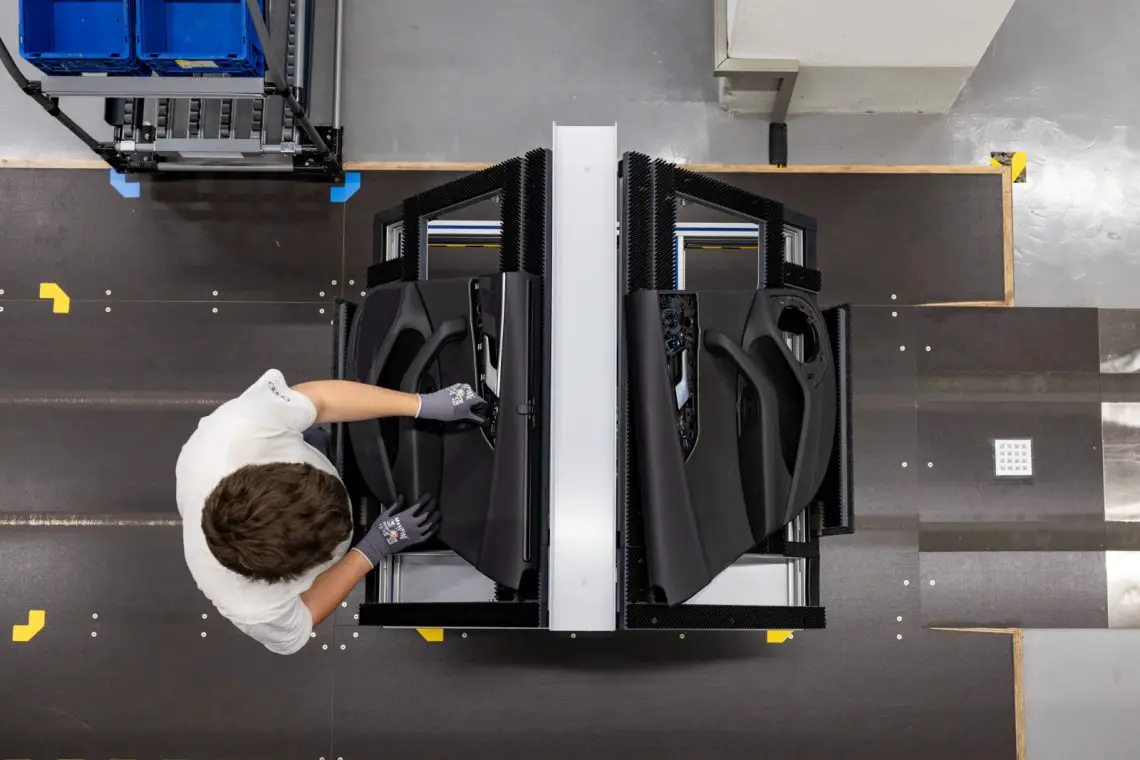
Roboter-Hund
In der gleichen Halle treffen wir Spot, einen Roboterhund. Spot ist eine Schöpfung von Boston Dynamics, einem amerikanischen Unternehmen, das auf Technik und Robotik spezialisiert ist. Spot geht im Internet regelmäßig viral, weil der Roboter fast wie ein echter Hund aussieht. Audi nutzt den gelben Hund, um eine Bestandsaufnahme des Fließbandes zu machen. In der Vergangenheit benötigten die Mitarbeiter rund drei Wochen, um 100.000 m2 im Audi-Werk zu inventarisieren. Spot, der Roboterhund, braucht dafür nur 48 Stunden. Er ist wendig und findet seinen eigenen Weg durch die Fabrik. Es braucht auch keinen Schlaf, nur eine gelegentliche Aufladung.
Er ist mit einem Hightech-Scanner des deutschen Technologieunternehmens NavVis ausgestattet, der die gesamte Umgebung in 3D erfassen kann. Das Ergebnis ist eine äußerst detaillierte 3D-Rekonstruktion der Fabrikhalle. Als ob Google mit seinem Maps-Auto hindurchgefahren wäre. Die Mitarbeiter können an ihren Computern virtuell durch die Fabrik gehen und sehen, ob Wartungs-, Lack- oder Ersatzteile nachgekauft werden müssen.
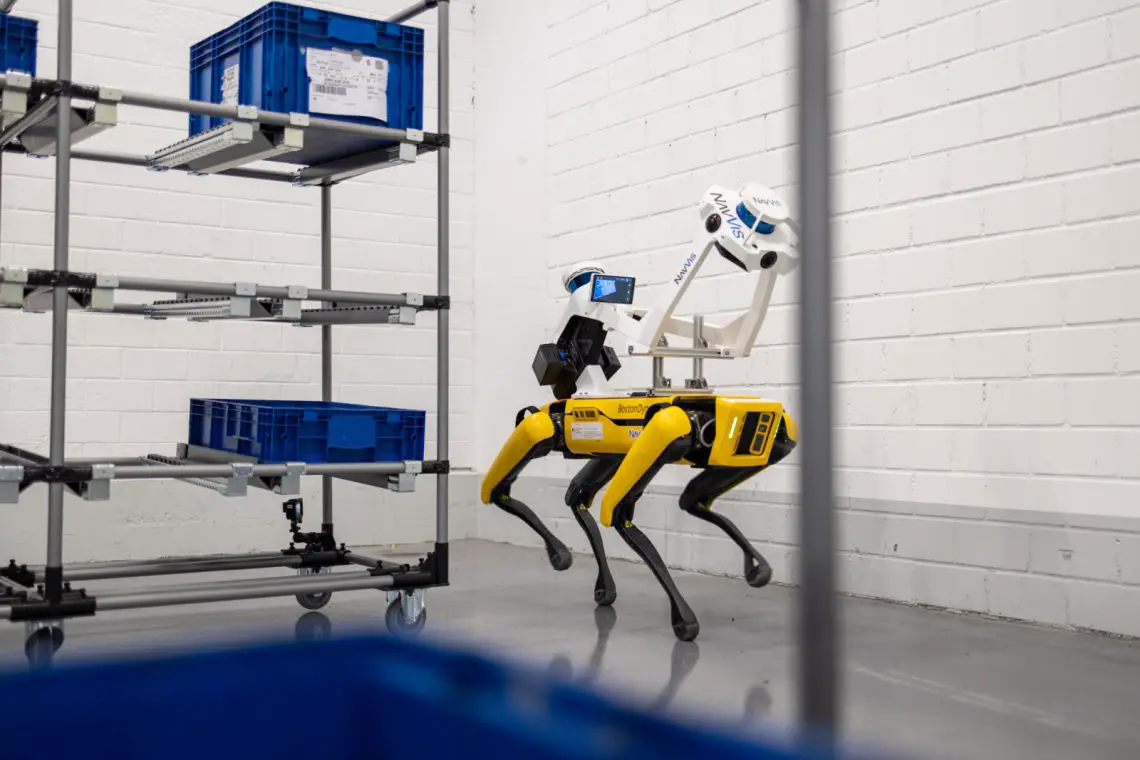
Künstliche Intelligenz
Es gibt noch mehr langweilige Aufgaben, die von Menschen im Audi Werk nicht mehr ausgeführt werden. So hat die Marke beispielsweise ein Pilotprojekt gestartet, bei dem künstliche Intelligenz (KI) die Qualität von Schweißpunkten überprüft. Rund 5.300 Schweißpunkte sind nötig, um die Teile in der Karosserie eines Audi A6 zu verbinden. Bisher prüften die Mitarbeiter in der Produktion die Qualität der Schweißpunkte stichprobenartig mit Hilfe von Ultraschalluntersuchungen. In dem Pilotprojekt wird jedoch KI eingesetzt, um Abweichungen automatisch zu erkennen, ohne dass die Produktionslinie angehalten werden muss.
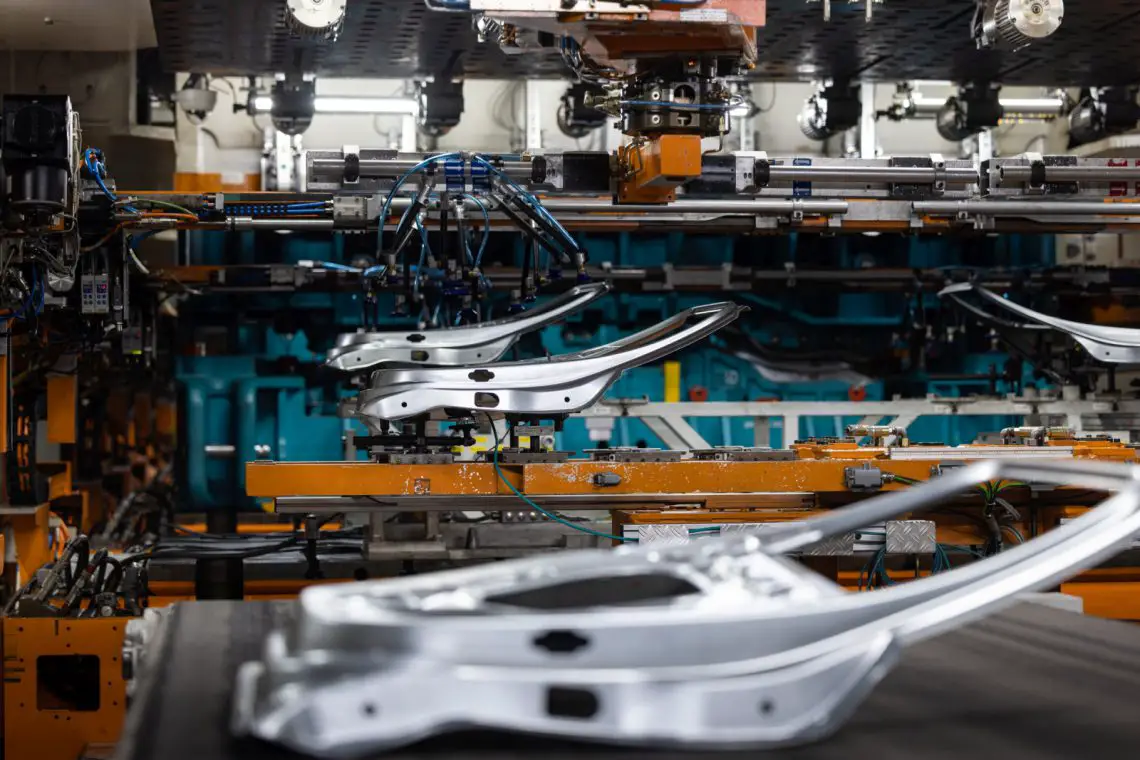
Nachhaltigkeit
Das Audi-Werk in Ingolstadt verbraucht in einem Jahr etwa so viel Energie wie eine mittelgroße Stadt. Schließlich braucht man eine Menge Energie, um aus einem Stahlblock ein fahrendes Auto zu machen. Um Energie zu sparen, hat Audi das Tool Energy Analytics entwickelt. In dem Tool werden alle Energieverbräuche im Betrieb erfasst und transparent gemacht. Zum Beispiel, wie viel Energie die Schweißgeräte verbrauchen, aber auch, was die Beleuchtung und Belüftung in den Gebäuden an einem normalen Tag verbraucht. Wenn der Verbrauch plötzlich in die Höhe schießt, können die Mitarbeiter genau sehen, welches Gerät dafür verantwortlich ist, und sofort Maßnahmen ergreifen. Bis 2021 konnte das Energy Analytics Tool bereits regelmäßig unnötigen Stromverbrauch aufspüren und 37.000 MWh einsparen. Damit kann man in einem Audi E-Tron GT eine Menge Kilometer zurücklegen.