How MINI sustainably produces the new MINI Countryman
MINI Countryman: transformation to electromobility
MINI hopes to produce the new Countryman primarily in a sustainable manner. Factory Director Petra Peterhaensel and Sonja Hengstler, Project Manager for the new MINI Countryman, are responsible in Leipzig for the transformation to electromobility and the sustainable production of electric drive components and complete vehicles.
Built alongside other BMWs
A core of 5,600 employees produces about a thousand vehicles a day. The new MINI Countryman rolls off the assembly line in Leipzig along with the BMW 1 Series, the BMW 2 Series Gran Coupe and the BMW 2 Series Active Tourer. This makes this location the first plant to produce models from both BMW and MINI on the same production line.
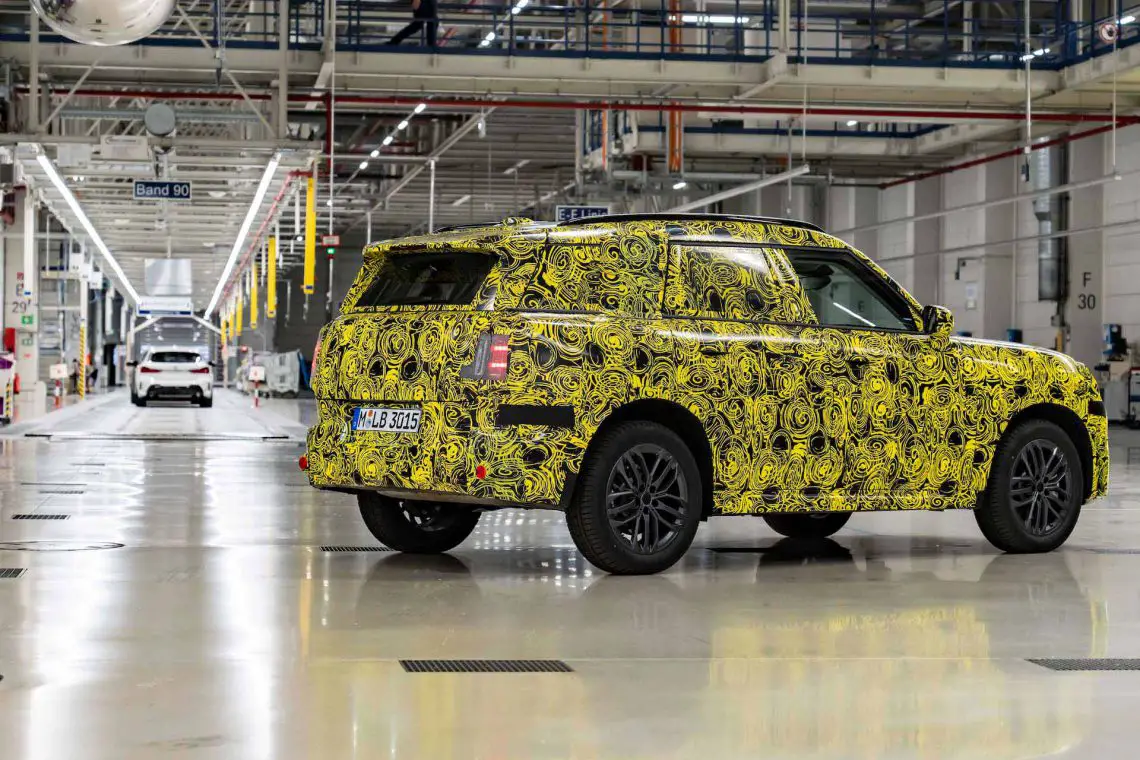
2030: electric MINIs only
Already, one in five MINIs is electric and in the Netherlands even one in four MINIs. The new Countryman – which rolls off the assembly line starting at the end of this year – is going to boost sales of electric MINIs. Starting in 2030, MINI will produce only battery-electric cars.
Investing millions of dollars
By the way, the batteries for the all-electric MINI Countryman come from the factory’s own production facilities. To that end, BMW Group is further expanding its production capacity for electric drive components at the Leipzig plant. Eight production lines will be added before 2024, an investment of more than 800 million euros.
The future production site for these components is 150,000 m2 in size and is a sustainable investment in the plant’s future viability. The expansion also provides job security for employees and even additional jobs. More than a thousand new employees will be hired for 2024 to produce the components for electric models.
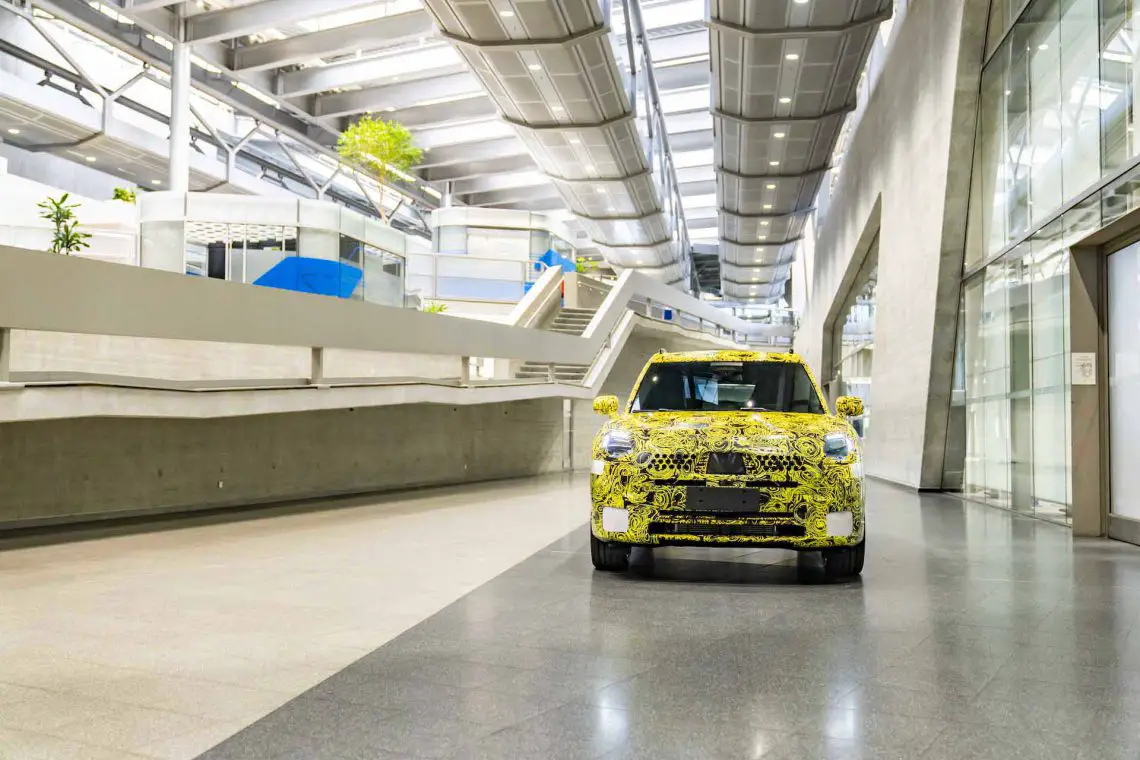
Sustainable production
The Leipzig plant has four 190-meter-high wind turbines located on the plant site. They generate some of the energy needed for car production. Wind power generated 21.9 GWh of electricity in 2021. This is equivalent to the annual energy consumption of more than five thousand three-person households. Since 2017, the plant has been temporarily storing the generated energy in battery storage consisting of nearly seven hundred batteries from the BMW i3.
Hydrogen filling stations
“Our vision for the Leipzig plant is to make production completely emission-free by replacing fossil fuels with hydrogen. Our Leipzig plant is the first car plant in the world to use a newly developed combustion technology in the paint shop, which uses green hydrogen instead of natural gas. We have also been using hydrogen for plant logistics since 2013. Currently, five hydrogen filling stations meet the energy needs of more than 130 industrial hydrogen trucks with fuel cells – the largest fleet of vehicles in Germany,” emphasizes Plant Director Petra Peterhaensel.
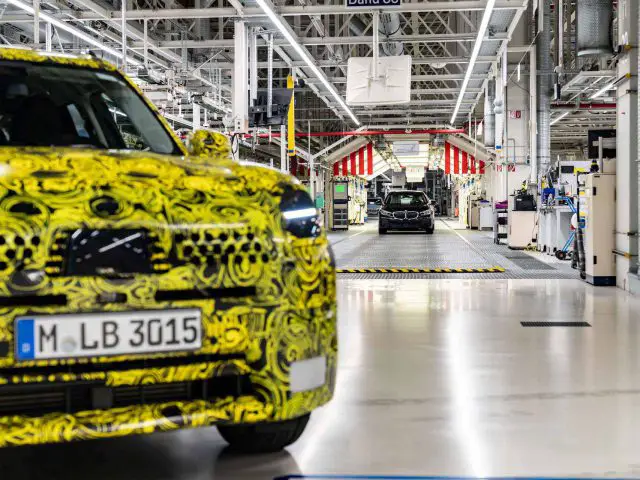
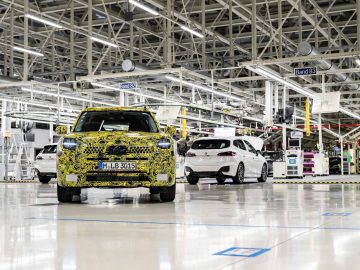
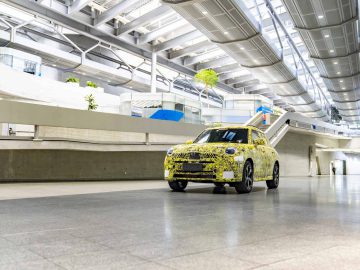
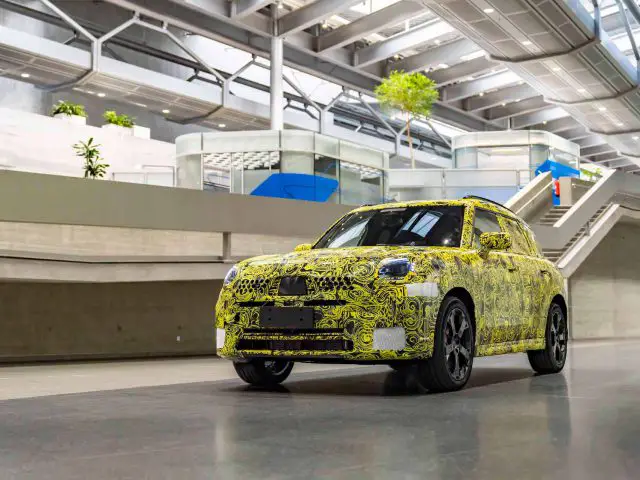
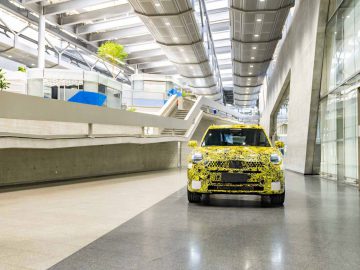
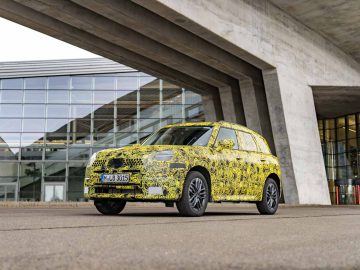