Photo report: Why the Alpine factory is different from other car factories
Manufacture Alpine Dieppe Jean Rédélé
It is the pride of Dieppe: the Alpine factory. Or as the factory is officially called: Manufacture Alpine Dieppe Jean Rédélé. You immediately notice how proud they are of the sports car brand when you drive into Dieppe. On the first traffic circle you encounter is a large, illuminated Alpine logo with an old and new Alpine A110 next to it. In front of it is a large glass sign that reads “Made in Dieppe. When French people post something in English on a sign, you know they mean it.
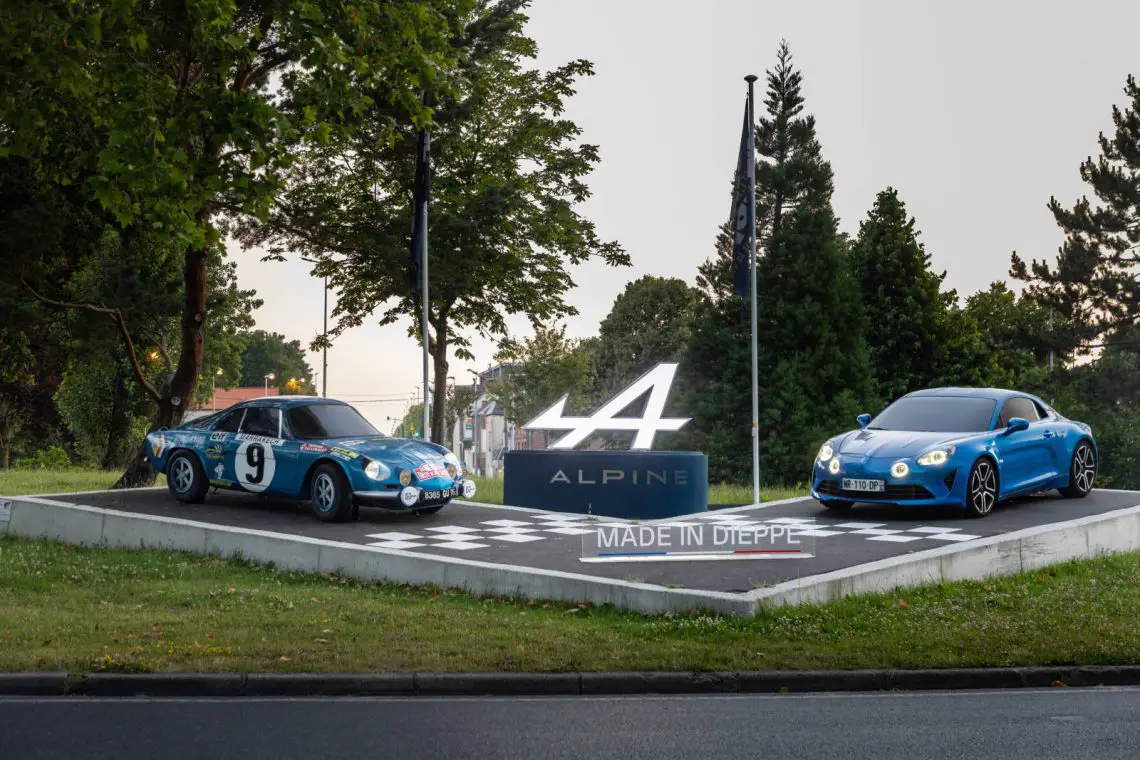
Dieppe
Alpine has a long history in Dieppe. Alpine was founded in 1955 by Jean Rédélé, whose favorite playground – the Alps – inspired his brand’s name. Alpine really took off when the original A110 appeared in 1962. At that time, Alpine and Renault were already working closely together. Thus, the models were sold and serviced by Renault dealers. The Alpine factory in Dieppe dates back to 1969. Two years before the A110 began its glorious victory tour in the rally world. In 1971, Alpine took the podium of the famous Rally of Monte Carlo and won it again in 1973, the year Alpine was crowned world rally champion. In that year, the brand was also fully incorporated into Groupe Renault.
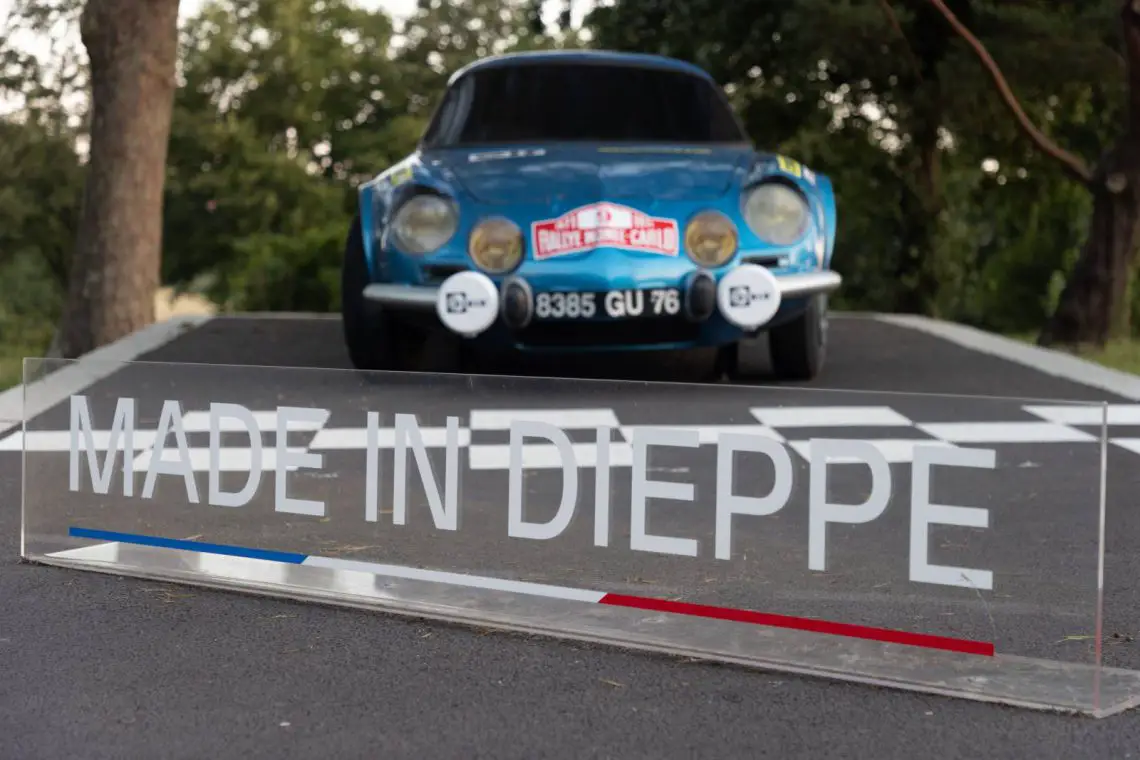
Alpine A610
The A110 was succeeded in the 1980s and 1990s by the A310 and A610, respectively. The models never became as popular as the 1970s A110, and in the mid-1990s Renault pulled the plug on the sports car brand. The lights at the Dieppe plant – by then wholly owned by Renault – remained on. The A610 no longer rolled off the assembly line there, but other sporty models from Renault did, such as the Clio Williams and Renault Sport Spider. Other (sometimes legendary) models such as the Renault 5 Turbo, 9 Turbo, 11 Turbo, Clio II and III RS, Espace, Mégane Cabriolet and Mégane RS were also all assembled at the Dieppe factory.
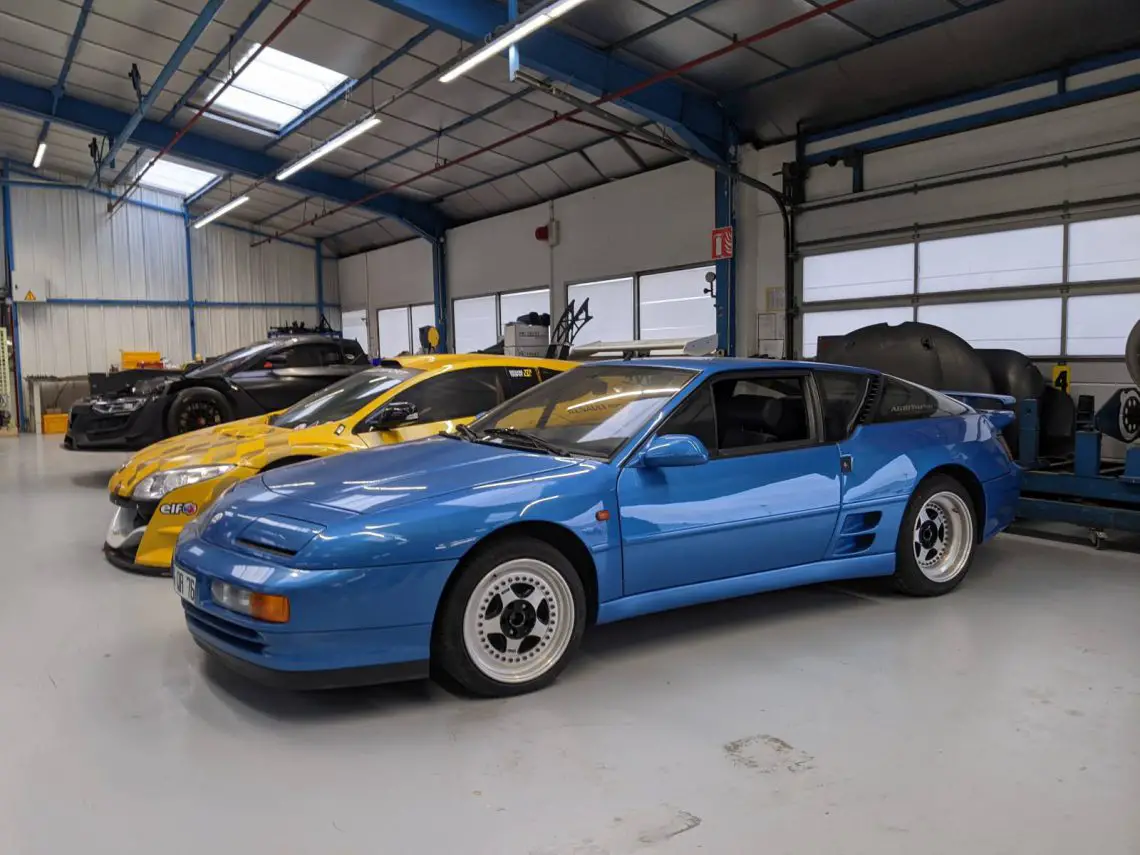
Reborn
In February 2016, Renault officially announced the relaunch of Alpine at a press conference in the port of Monaco, the place where the brand celebrated two Monte Carlo Rally wins in the 1970s. The announcement also marked the brand’s return to the French coastal town, where the new A110 would go into production. Although the soul of the brand had never really left Dieppe, because even after the production stop in the 1990s, the Alpine logo never disappeared from the factory wall.
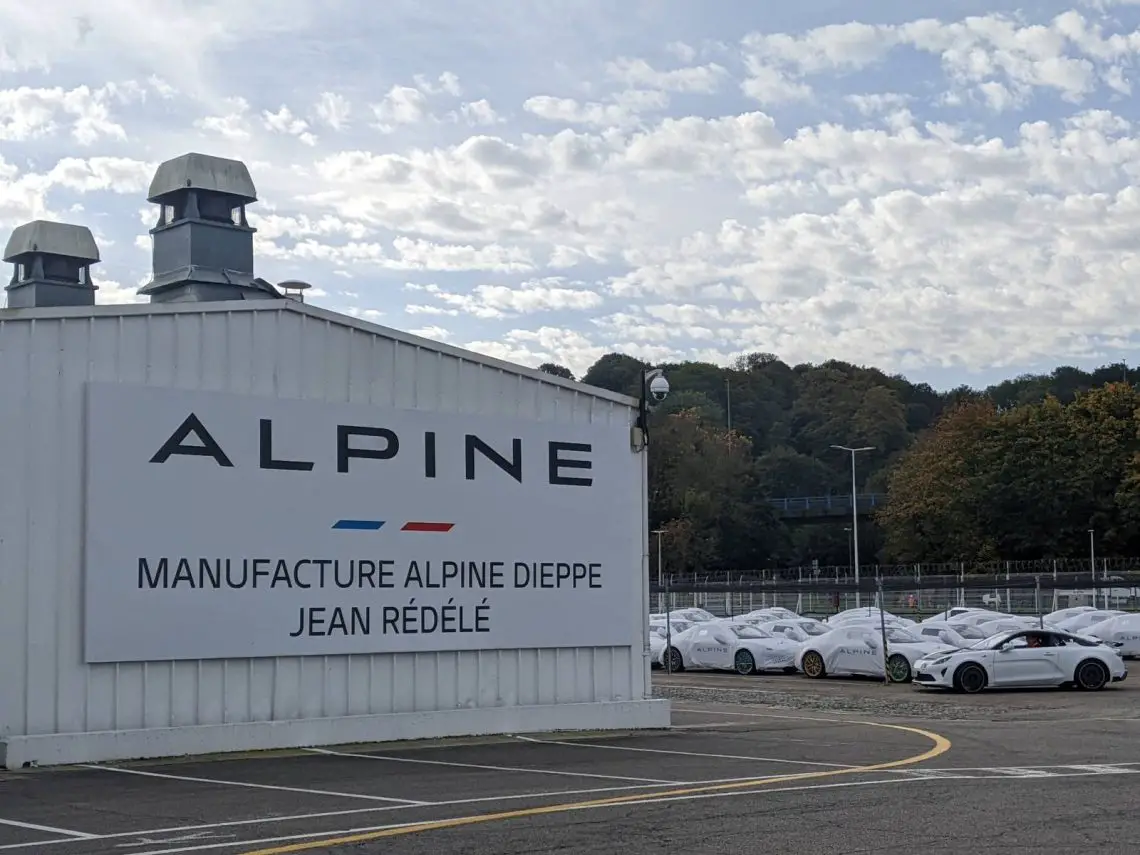
Alpine A110
Since December 1, 2017, the modern reincarnation of the illustrious A110 from the 1960s and 1970s has been rolling off the assembly line in Dieppe. Over 14,000 new Alpine A110s are now on the road. Dieppe employs 400 men, producing eighteen brand-new A110 models every day.
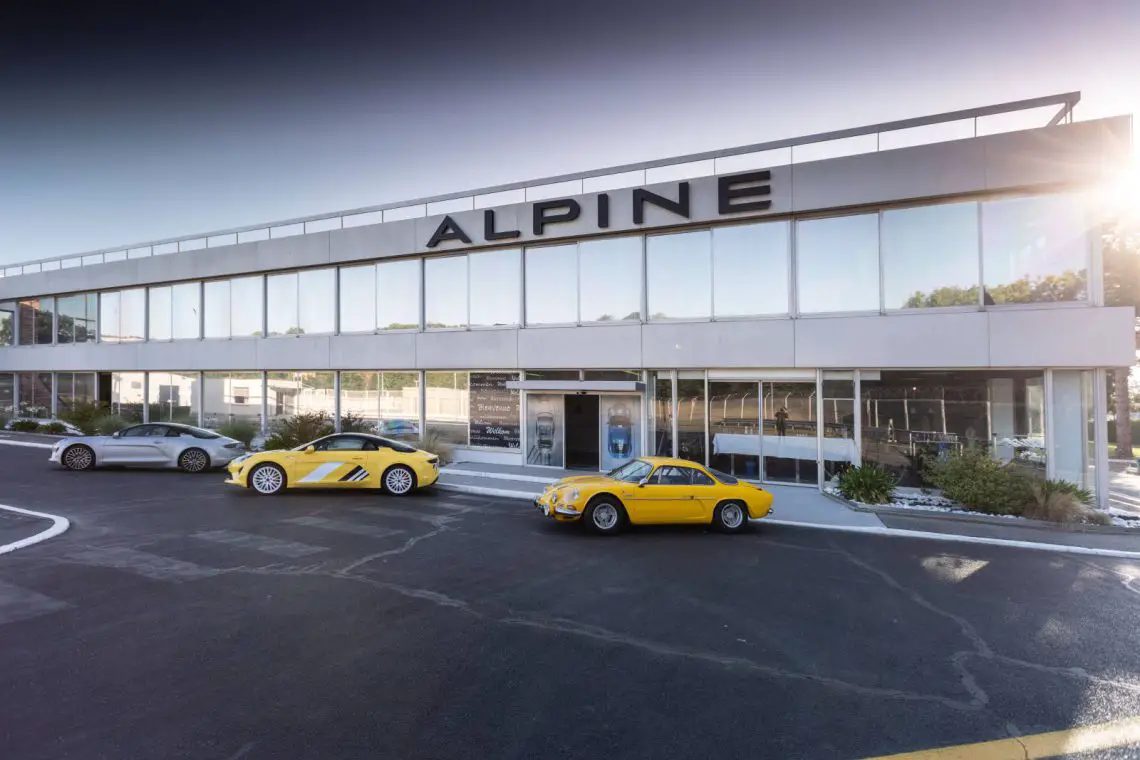
Handmade
During our factory tour, we get to see the entire production process of the new A110. The plant operates differently from other Renault production sites. This is evidenced by the fact that “only” eighteen cars are built per day. There is a lot of handwork involved in building an Alpine A110. That’s how it is with exclusive sports cars.
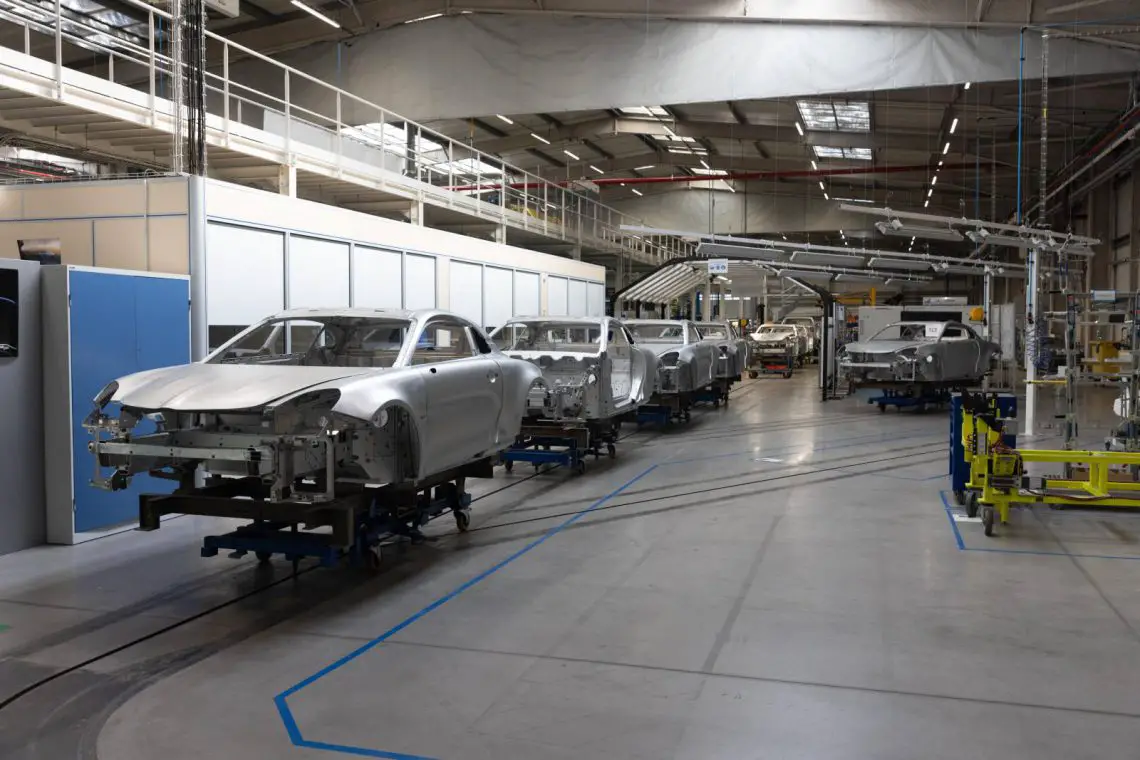
Robots
There are also fewer robots present than in a traditional car factory. The robots that do attend often work with staff. For example, there is a gluing robot, which glues the chassis in places where workers have difficulty reaching. Moreover, he does it at a high pace. Glue you say? Yes indeed, the Alpine A110 uses an aluminum body, which is fully bonded to save weight.
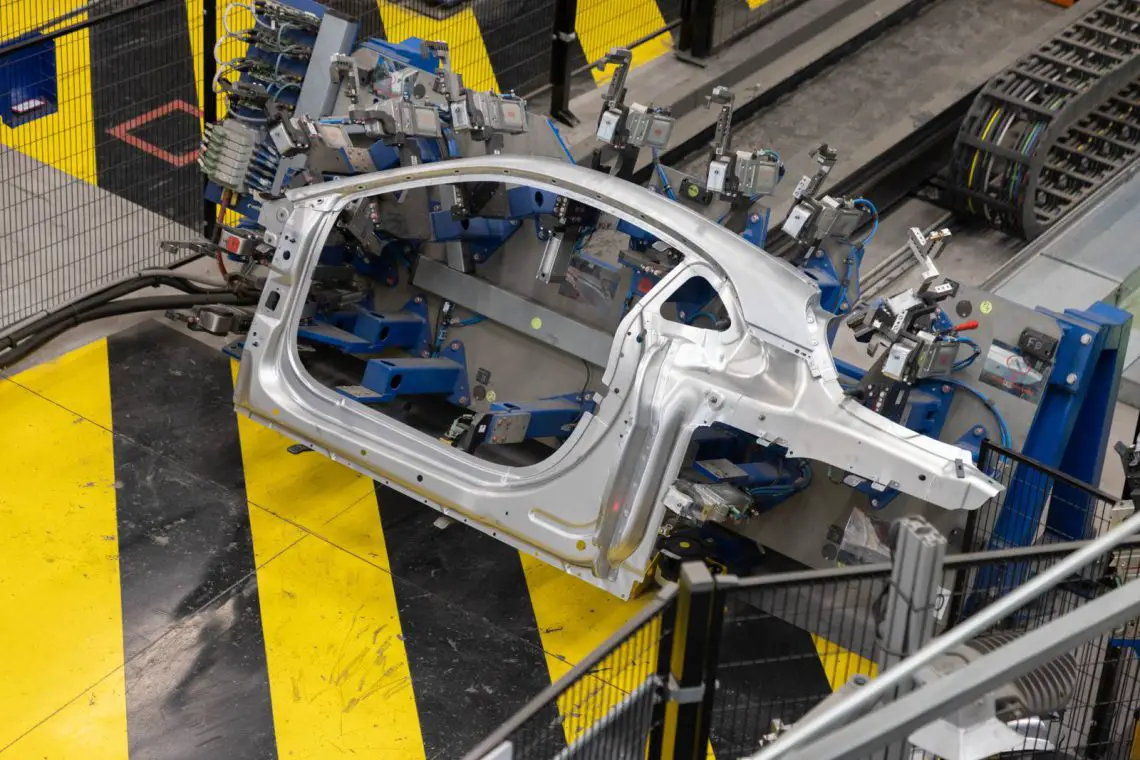
Vakwerk
After the self-supporting chassis is largely glued together, robots assemble the roof, after which workers assemble some side panels and the hood and tailgate. With measuring equipment and a rubber mallet, workers carefully run all the panels and check that they fit together seamlessly. Then the car gets a push toward the next hall.
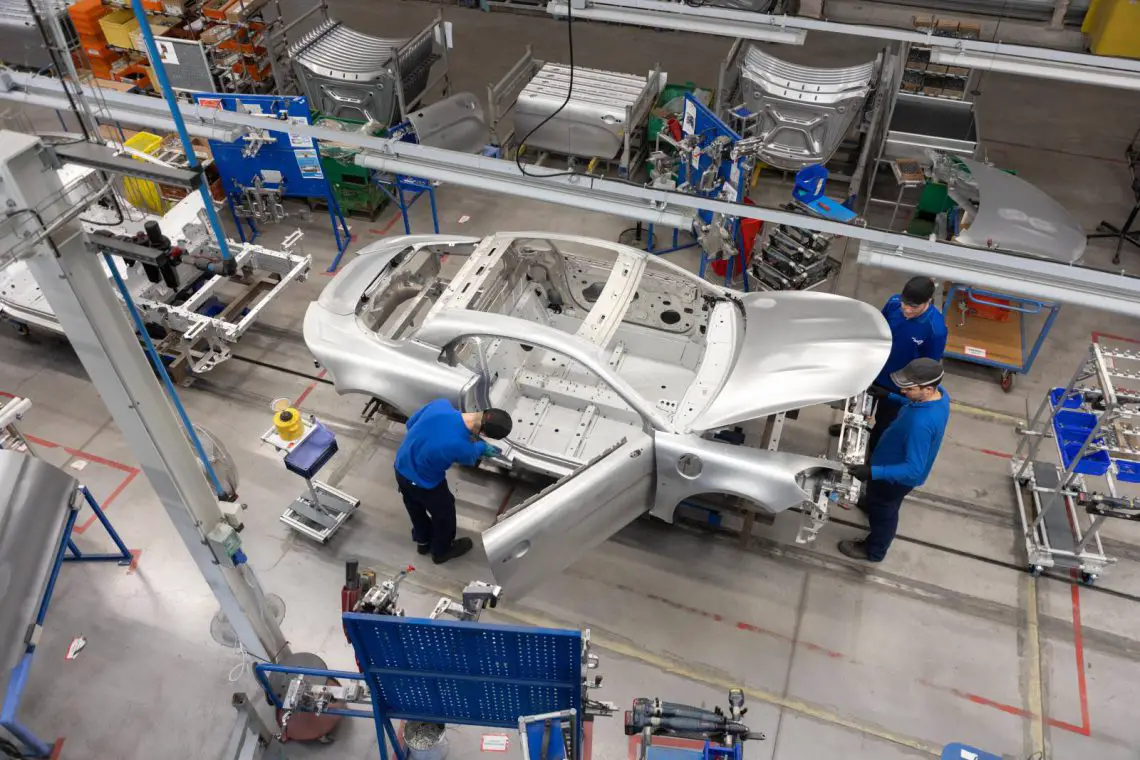
Paint shop
Once all the sheet metal parts have formed a complete body, it’s time for a lick of paint. This, too, is largely done by hand. After an anti-corrosion bath and a coat of primer, it is time for a sanding, after which robots apply the body color. Not surprisingly, the most frequently chosen color is blue, Alpine’s house color. But every now and then we come across a yellow, red and black A110 at the factory.
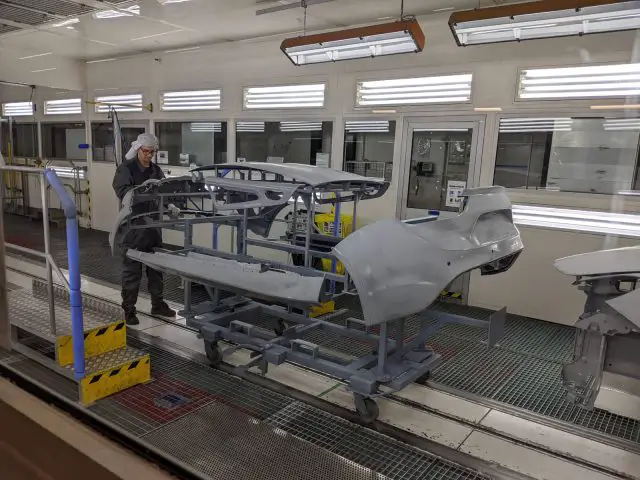
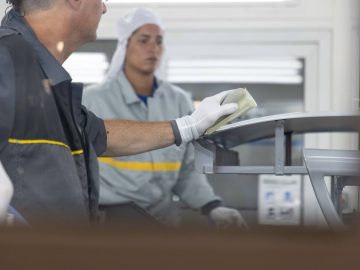
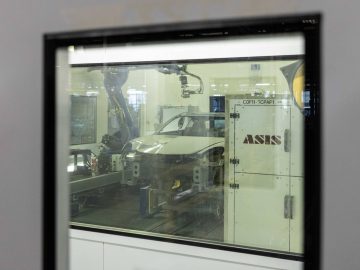
Marriage
Then it’s time for the final assembly. In the factory’s largest hall, A110 models literally fly around your ears if you’re not careful. The chassis, interior, windows and everything else a car needs come together here. We get to witness the so-called marriage: the moment when the body and the power source are connected. Slowly, a robot lowers the body over the 1.8-liter turbocharged engine and rear subframe, then workers screw things together.
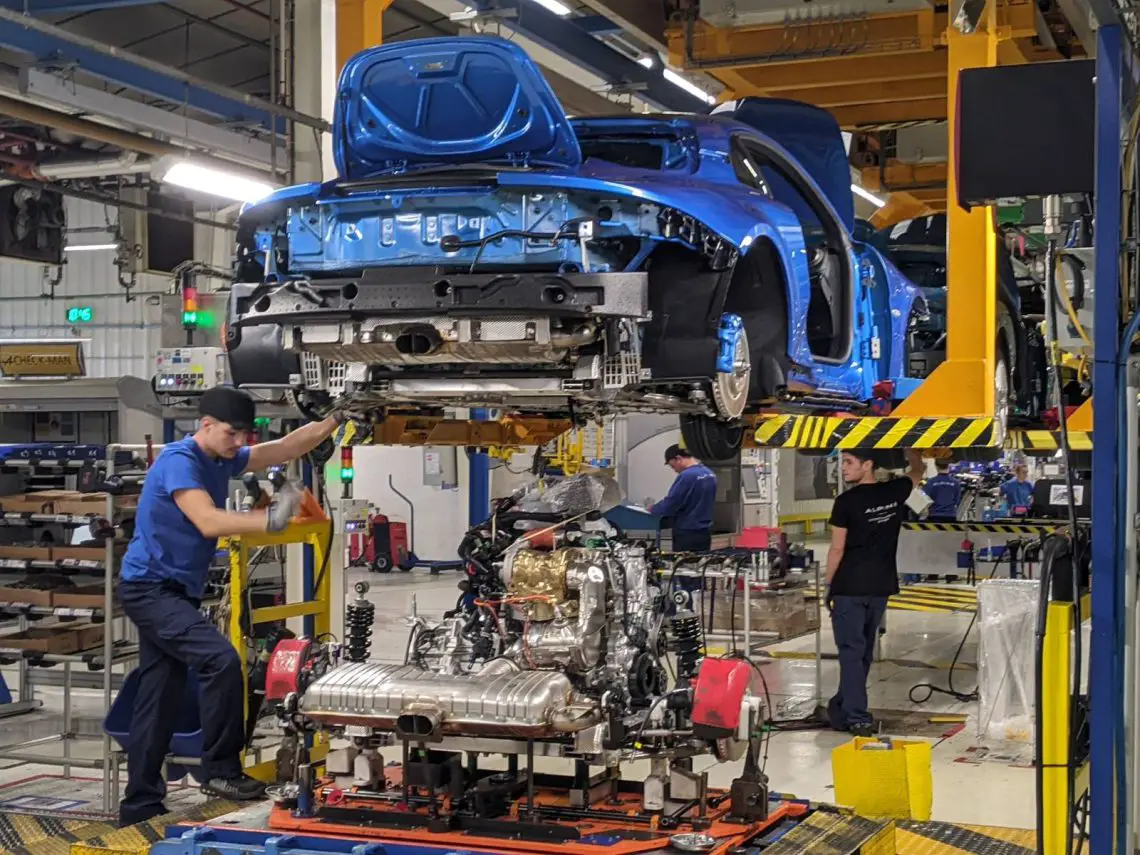
Light tunnel
In a light tunnel, an employee walks the car through dozens of points during the final “quality check. Then the car drives out of the factory under its own power, after which it undergoes dynamic quality control. During these tests, Alpine looks to see if the car drives the way an Alpine should: tight but nimble. You can read more about the driving experience of an A110 HERE.
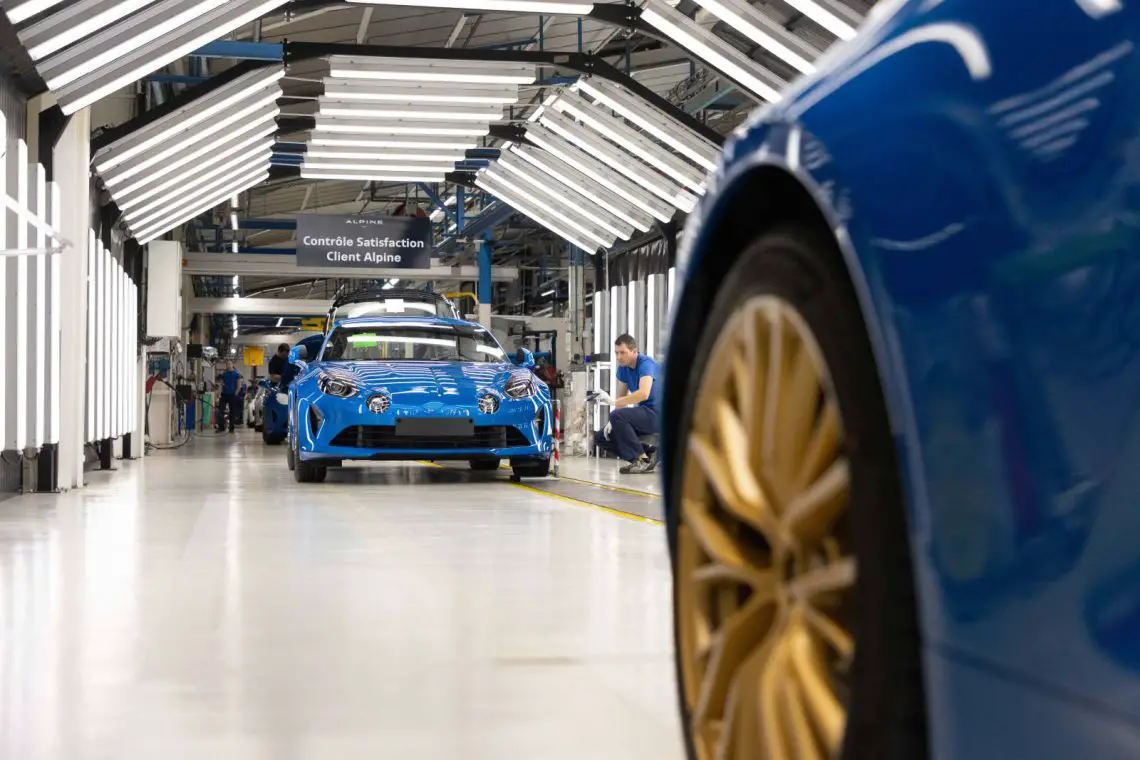
Electrification
In 2024, Alpine is changing course significantly. The brand will then launch its electric future with the introduction of a B-segment hatchback, which will be based on the new Renault 5. In 2025, the brand will introduce the first model to roll off the assembly line in Dieppe: the Alpine GT X-Over. During our visit to the factory in the French coastal town, we get little information about this new electric crossover. However, the French do let it be known that they have no qualms about electrifying the brand. Alpine expects to increase future production sevenfold at best, thanks to high demand for electric cars and a wider model range. And the A110? It will not disappear from the market for a second time. Indeed, its – obviously all-electric – successor is scheduled for 2026.
Also read: