Nissan Qashqai and Sunderland: inextricably linked
Nissan in Sunderland: the history in a nutshell
In the 1980s, Japan’s Nissan plants are running up against their maximum capacity. The brand must look for a new production site to serve the rapidly growing demand in the European market. At the same time, the Northeast of England is facing high unemployment. Moreover, in the form of a former RAF airfield next to the town of Sunderland, just south of Newcastle upon Tyne, a geographically favorable location is found. A win-win situation.
In 1984, Nissan Motor Manufacturing (UK) Ltd was established, also known as NMUK for short. In 1986, car production begins in a modest factory hall. This still involves painting and finishing so-called knock-down kits of the Nissan Bluebird. Roughly speaking, bare bodies and parts were delivered and the factory builds a complete car from them. Scaling up soon followed, however, and in 1990 the then brand new Nissan Primera became the first model to be produced entirely locally. In 1992, it scaled up once more: the factory could now produce two models simultaneously, and the also brand-new Micra was added. Since 1999, three different models can be produced simultaneously.
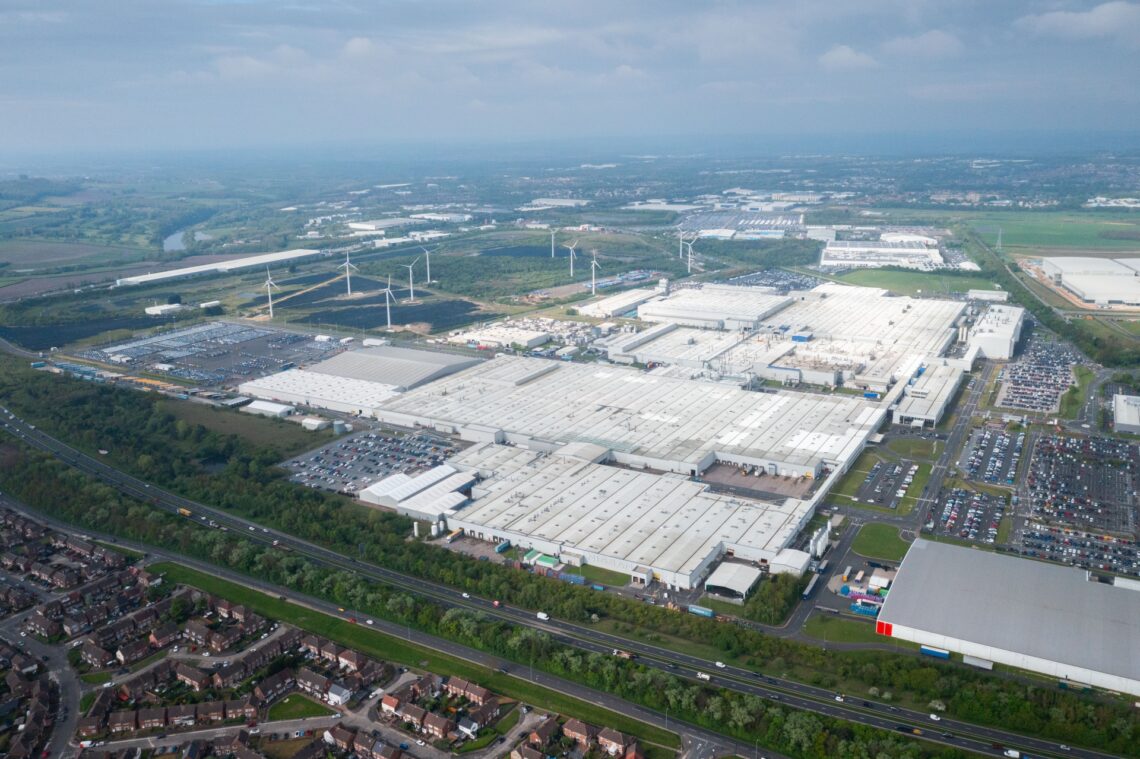
Nissan Qashqai provides breakthrough and salvation
The real breakthrough came in 2006, with the first Nissan Qashqai. The car is an immediate resounding success and the factory is forced to institute a night shift. Although the plant had to scale down during the 2008 financial crisis, the success of the Qashqai dragged them through. Anno 2024, NMUK in Sunderland is one of the most efficient car factories in the world, producing not only the Qashqai but also the Juke. Production of the LEAF is on hold for a while, in preparation for the new model generation.
Nissan also gathered for us some fun statistics to indicate the Qashqai’s success. For example, did you know that one in five cars produced in the United Kingdom since its introduction is a Qashqai? The factory has now produced more than 4 million Qashqais. The main outlet (20% of production) is the United Kingdom itself. Another fun statistic: if you plot the number against the area of the country, you are never more than 500 meters away from a Qashqai!
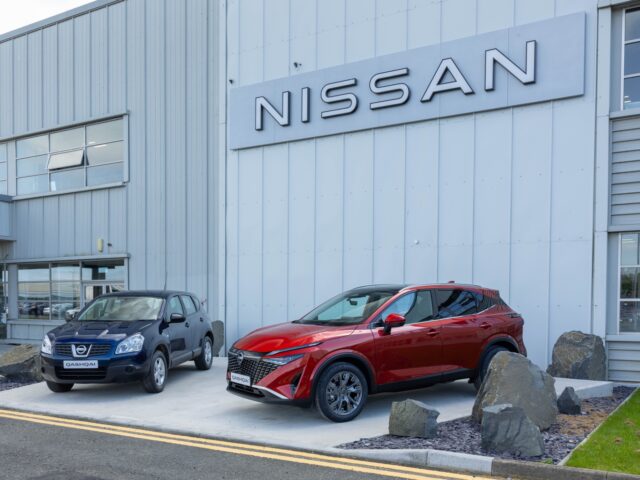
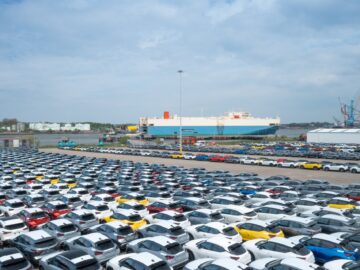
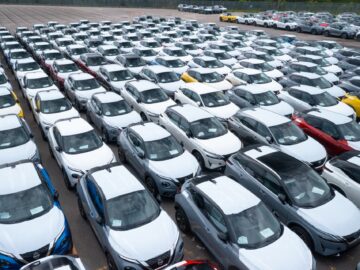
Nissan Qashqai is actually English
By the way, did you know that the Nissan Qashqai is actually a British car? All model generations were developed by Nissan Motor Great Britain and the Nissan Technical Centre Europe and designed by Nissan Design Europe (all three based at most 80 km from London). So production takes place in Sunderland, in the northwest of England.
AutoRAI.com is going to apply
Our factory visit begins with an application. That is, Nissan let us conduct the test for workers on the production line. A working environment was simulated with an “engine bay,” an “interior” and an “underside. In quotes, because they are only stellar. However, they mimic the working environment well. There are five tasks: assemble bolts (bolt, washer, washer, smaller washer, nut, tighten, next), snap on a row of plugs, push plastic caps into a bulkhead, assemble some exhaust rubbers, and assemble some on-board computers (bracket, module, another bracket, bolt, bolt, insert, bolt, bolt, next).
In itself simple tasks, but it has to be done several times in a row and we have only a little over ten minutes total for it. We passed the test, just barely. That doesn’t mean we can just join the production line. Passing this test only means that you have sufficient aptitude for it. A real applicant would undergo further training.
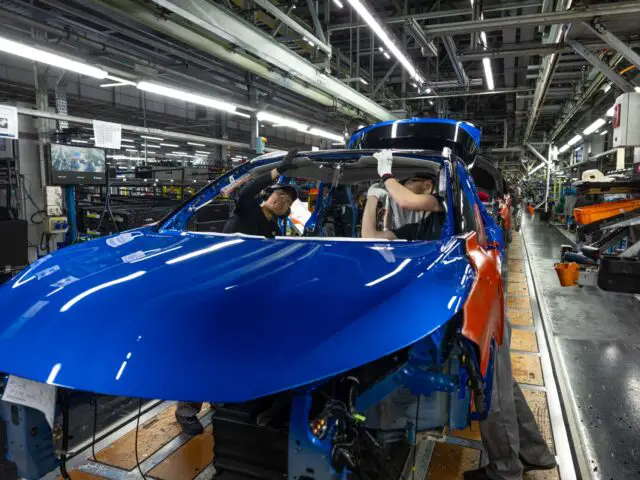
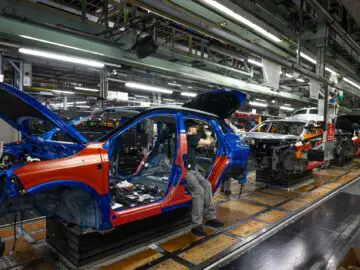
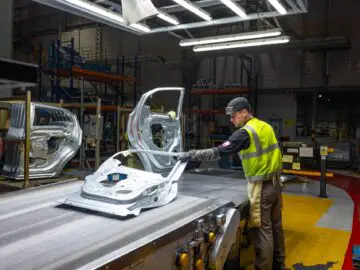
‘Old-fashioned’ handiwork
The manufacturing process of a car is broadly the same for every make and model. Yet sometimes brands have their own peculiarities, for example, because they take a slightly different approach to something than the competition. A special feature of the Nissan plant in Sunderland, for example, is that they produce almost everything locally these days. Raw materials about the only thing the factory gets supplied. Batteries are also produced locally.
Which brings us to the following: although much of the production process is automated, batteries in particular still involve a relatively large amount of manual labor. A kind of autonomous driving worktable will drive by, with a partially assembled battery pack on it and some parts yet to be assembled. A monitor at the workstation shows exactly which part goes where and even in what order the technician should tighten all the individual screws. If you want to tighten the wrong screw, the electric screwdriver simply refuses service.
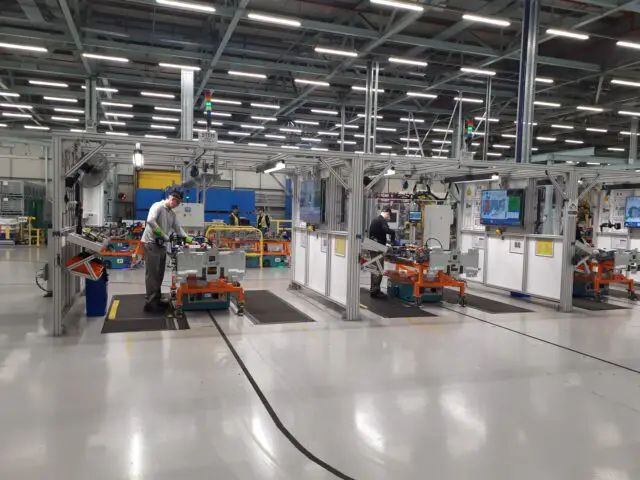
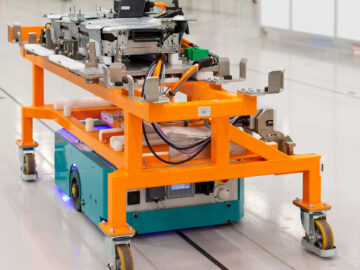
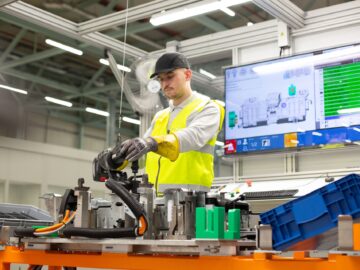
In short, as an assembler, you don’t actually have to think about assembly, you just follow the instructions on the screen. This begs the question of why this assembly process is still “manual. The simple version of the answer: the operations are still a little too complex for robots, but in five to 10 years this department could just be fully automated.
We also find handicrafts in other parts of the factory. Thus, they are real employees who check that the robots have assembled the bodies properly. Later in the production process in the paint shop: if someone has ordered a roof in a contrasting color, the rest of the body is taped off by hand (a job too precise for robots) and the roof is painted again.
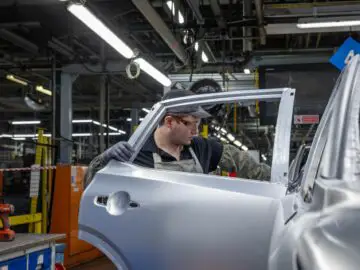
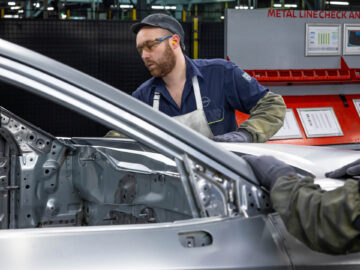
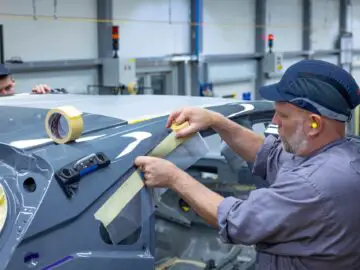
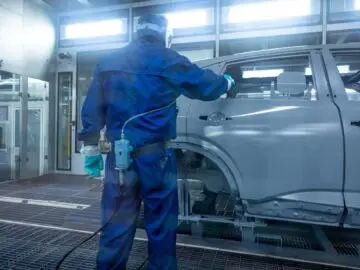
All mixed up
Also notable in the paint shop is that all the colors are simply painted “interchangeably. A red Qashqai follows after a gray one, a blue one, a black one, a white one, etc. The spray robots are so advanced that they can change colors in a matter of seconds, with no color residue blending in. Even in the spray booths, the cars do not “contaminate” each other. The cars are statically charged so the paint adheres better and an extraction system takes away the remaining haze. By the way, the captured paint is not thrown away, but collected and reused for purposes for which a lesser quality paint is sufficient. As a base for road markings and other exterior paint, for example.
That everything jumbles together in an orderly fashion is a recurring theme in the factory. In another assembly hall, we see Nissan’s Qashqai and Juke on the same production line, in different versions. From entry-level to top-of-the-line models, everything goes in seemingly random order. Still, the “brains” behind the assembly line know how to make sure that the right bumpers, dashboard, powertrains, etc. end up with the right bodies.
Comprehensive quality control
When the Nissans are completely finished, they will be tested extensively. That in itself is nothing special, because every manufacturer performs quality control. What is notable is that Nissan runs a 1.6 km test track with each one produced. Based on sampling, some specimens are subjected to even more extensive testing. All in all, each Qashqai produced undergoes some 1,000 quality checks. This way they can be sure that every Nissan produced is fully functional.
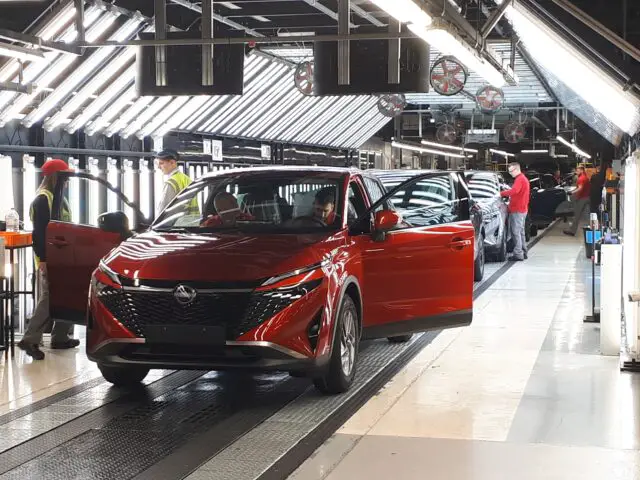
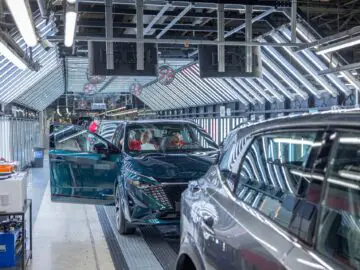
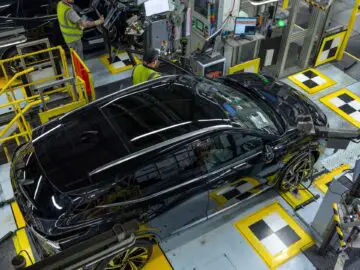
The coming years: (even) more electrification, including with new LEAF
Looking at Nissan’s future plans, there is obviously a lot of electrification there. Thus, for financial year 2026, the brand plans to introduce as many as 16 electrified models (that includes hybrid), compared to 14 fuel-engine-only models. Six of these models are coming to Europe and these are exclusively electrified models. Here, in fact, Nissan is working hard to become an all-electric brand. However, no concrete year has yet been attached to that target, partly because it depends on market demand.
Things get a little more concrete when we look at some recently presented concept cars. For example, the Hyper Punk Concept gives an impression of the new Nissan Juke and the Hyper Urban gives an idea for the next-generation Qashqai. So that will take some time, as both have only just been renewed. For the short term, we can expect a new, third-generation Nissan LEAF, though. About that, Nissan would only say that it will remain a C-segment car, but it will be “a little more crossover.” Furthermore, the brand does drop hints that the 2021 Nissan Chill-Out Concept could just be a preview of the new LEAF.
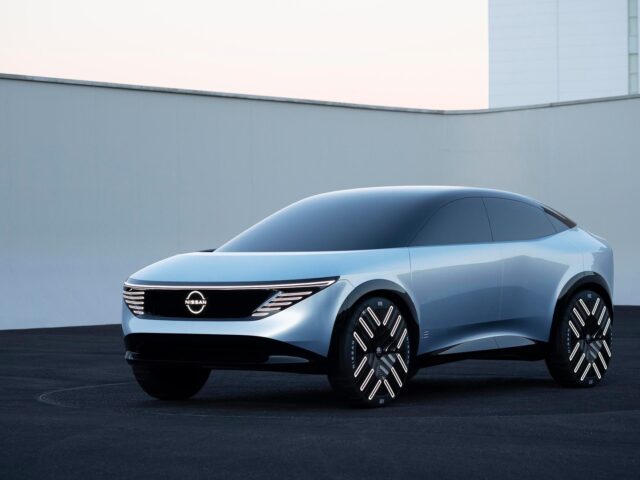
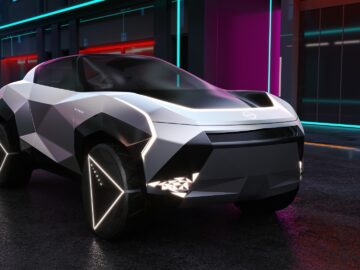
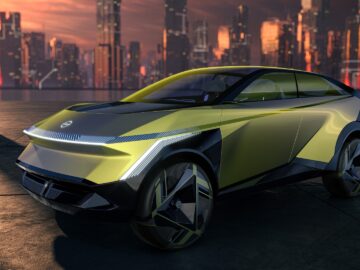